OnePlus factory tour: An inside look at how the OnePlus 6 is made
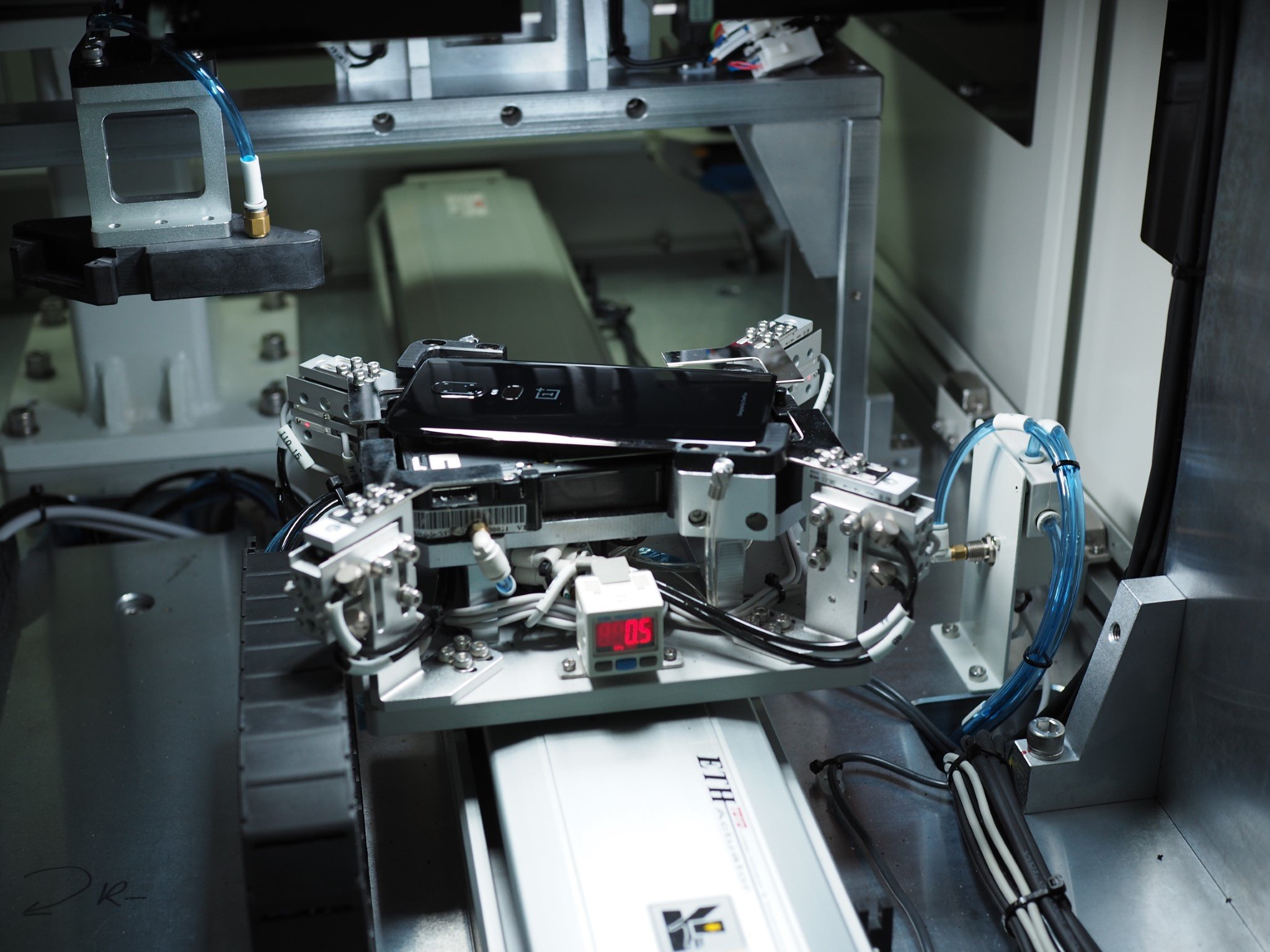
Over the last four years, OnePlus built up a name for itself as a company that caters to power users. OnePlus now sells in most major global markets, but it's India where the company has seen the most success to date. The Chinese company managed to overtake Samsung as the premium segment in the country earlier this year, a worthy accomplishment from a brand that's just four years old.
A lot of that comes down to the OnePlus 6, the company's latest phone. The OnePlus 6 stands out not because of the hardware — there are plenty of phones that offer similar specs — but mainly due to OnePlus' emphasis on delivering a clean software experience with OxygenOS. Combine that with OnePlus' obsession over speed, and you get a device that's one of the fastest available today. It doesn't hurt that the OnePlus 6 costs roughly half that of the Galaxy Note 9.
So when OnePlus asked me if I'd be interested in touring its factory to see how the OnePlus 6 is manufactured, I immediately jumped at the chance. OnePlus manufactures its phones at a factory an hour's drive away from Shenzhen, where its headquarters are located. The factory I visited is the main production line, and it also has other facilities around the globe that cater to needs in other markets.
With that out of the way, let's take a look at how the OnePlus 6 comes to life.
The assembly process starts off with the mid-frame. The mid-frame comes from a manufacturing facility that's located a few miles away, and the first bay in the assembly line houses a machine that drills a series of holes into the mid-frame. Then the panel is affixed to the front using adhesive, and the phone is then sealed in a case and tightened so the glue affixes evenly.
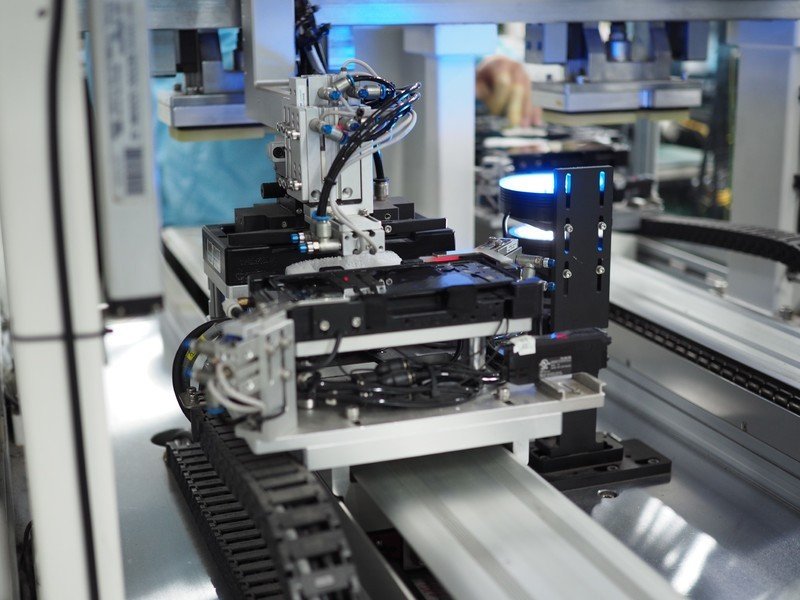
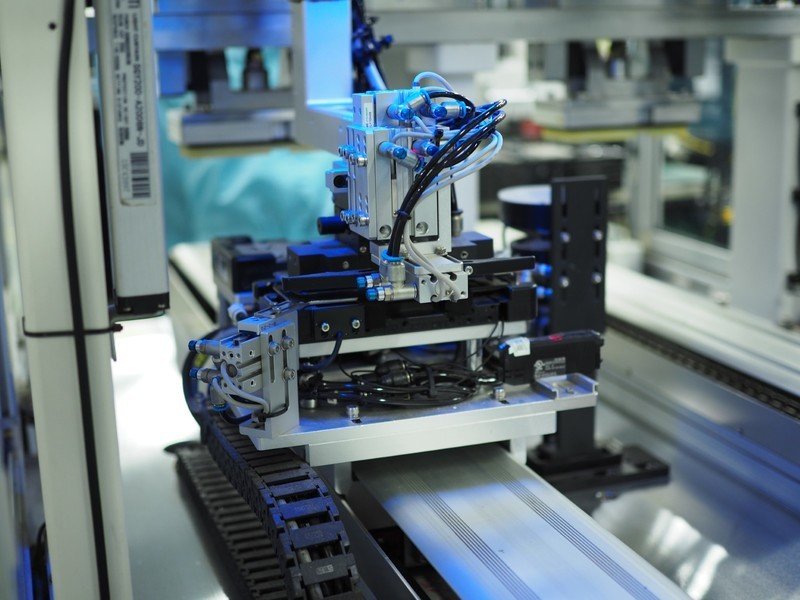
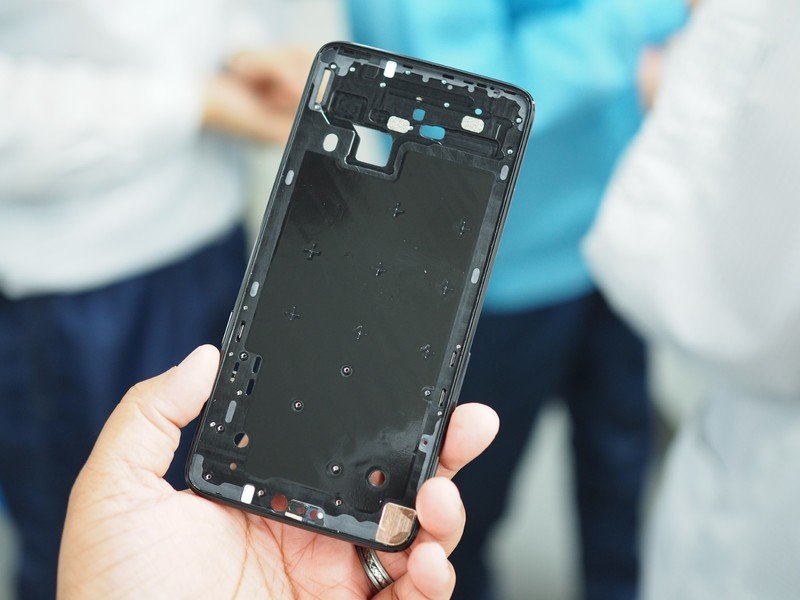
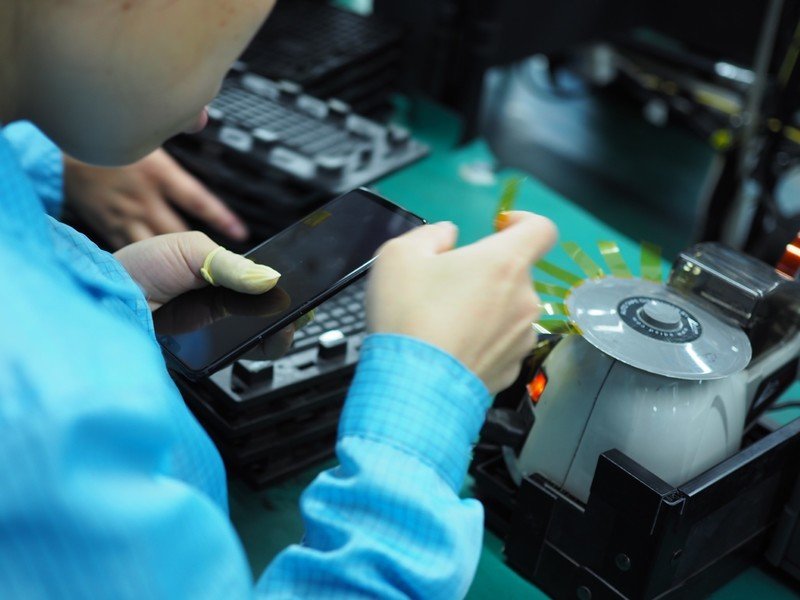
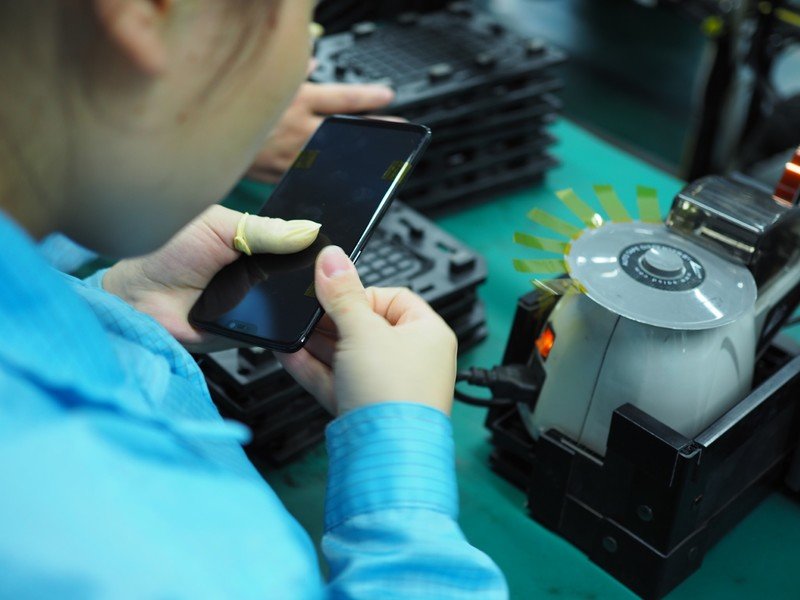
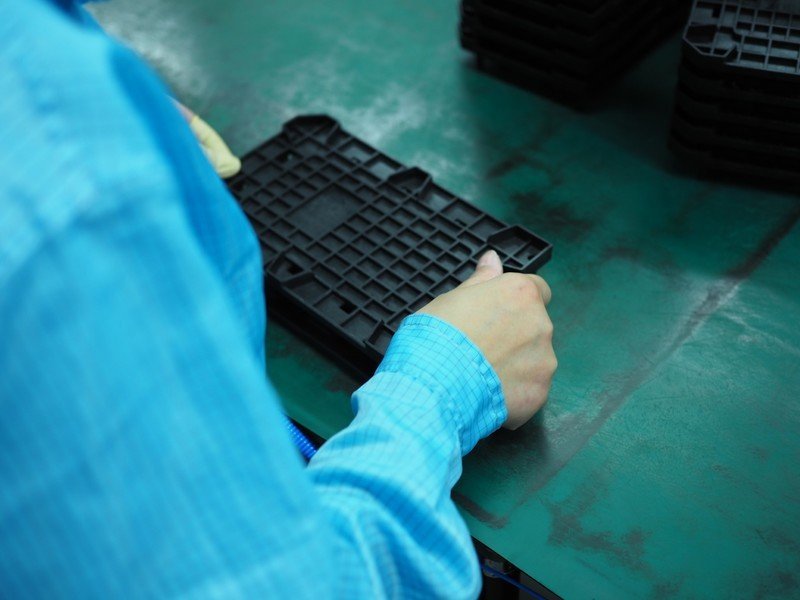
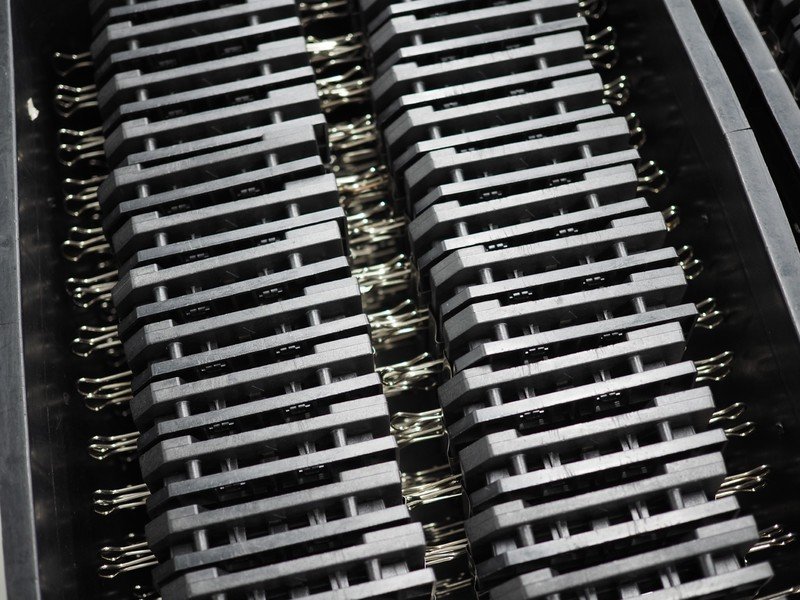
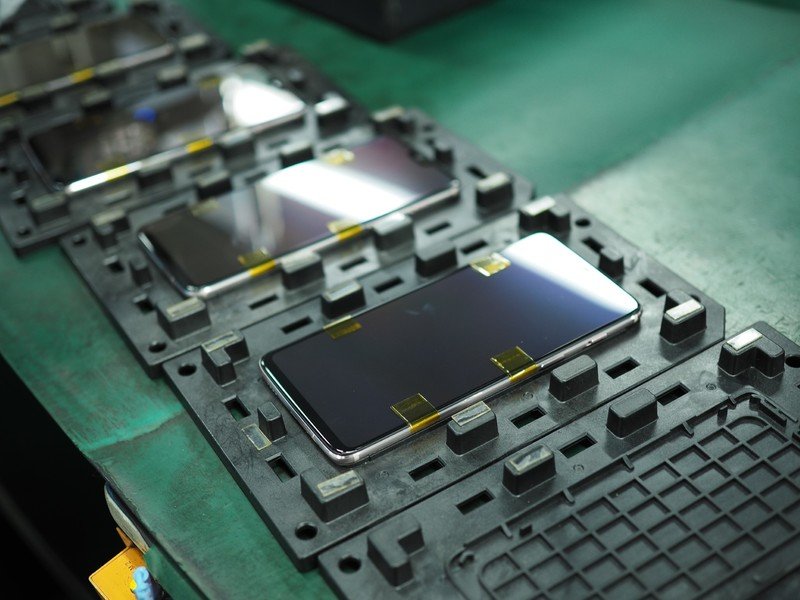
Once the panel is affixed firmly, it's time to hook up the connectors for the USB-C charging port at the back. Then the haptic motor is connected to the back of the device, to the left of the USB-C port.
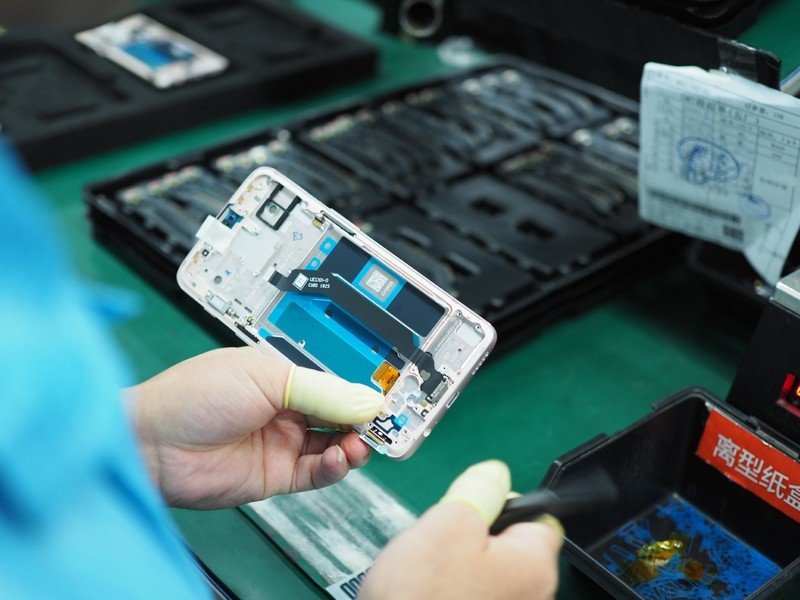
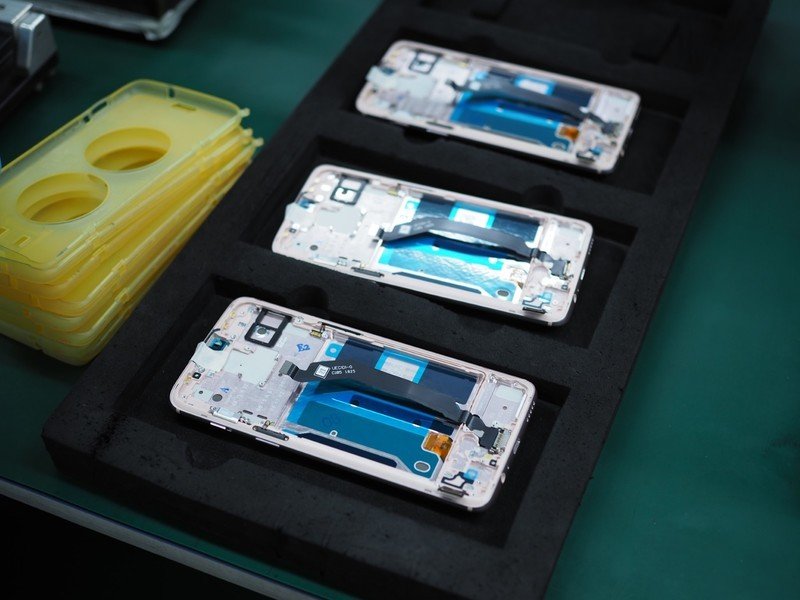
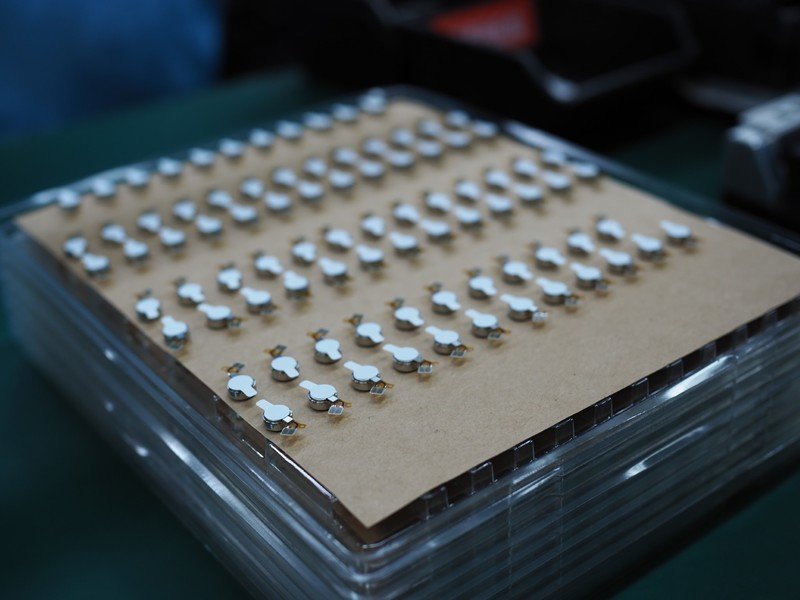
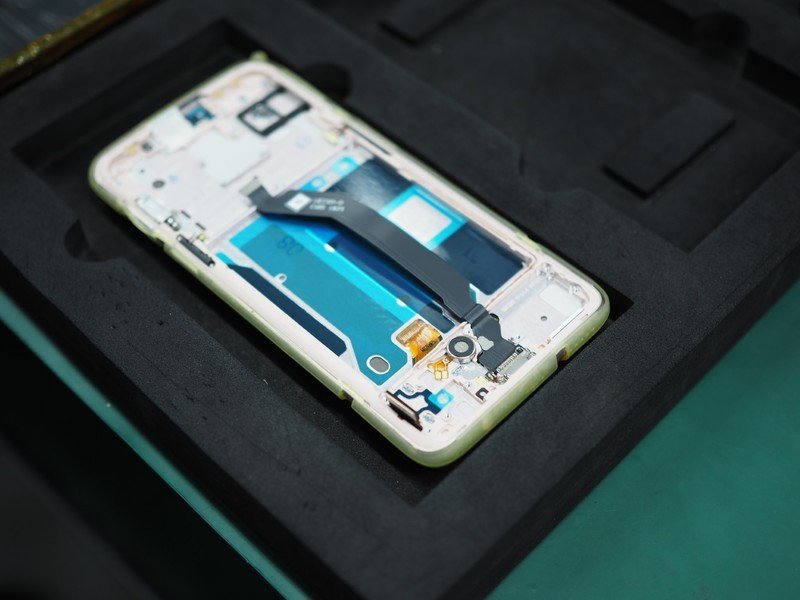
Next up is a machine that checks the display for any issues. As the mainboard isn't hooked up to the phone yet, it is connected to an external machine that cycles the panel through a gamut of colors and scenes to make sure the panel doesn't have any defects. After the display tests are finished, the device is placed in a case that covers a sizeable portion of the screen to prevent it from taking any damage while on the assembly floor.
Be an expert in 5 minutes
Get the latest news from Android Central, your trusted companion in the world of Android
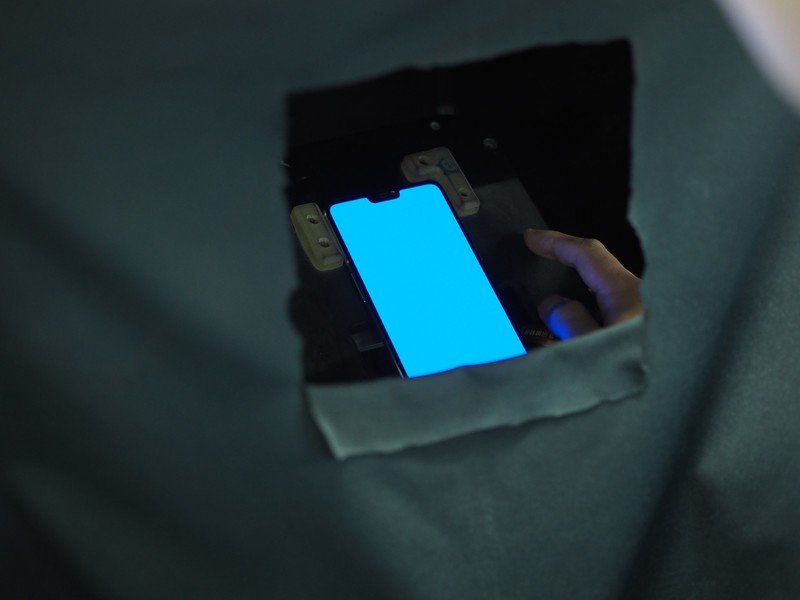
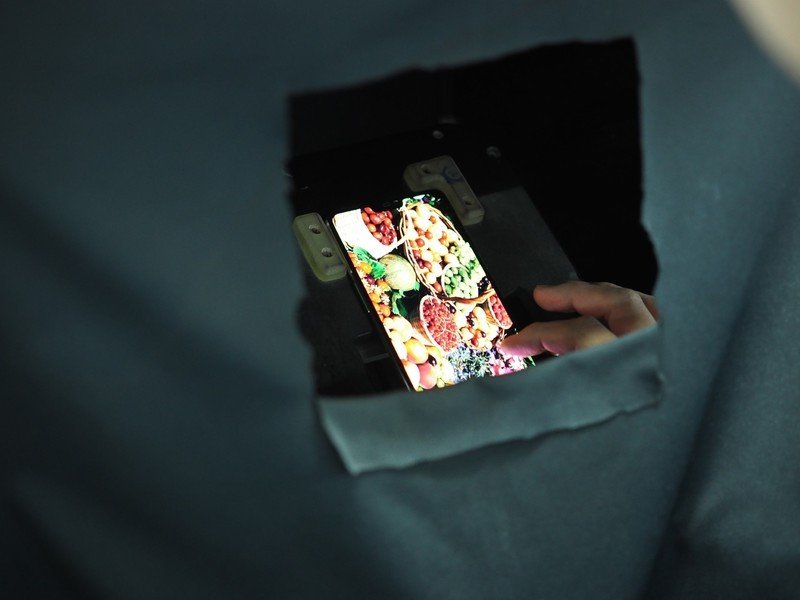
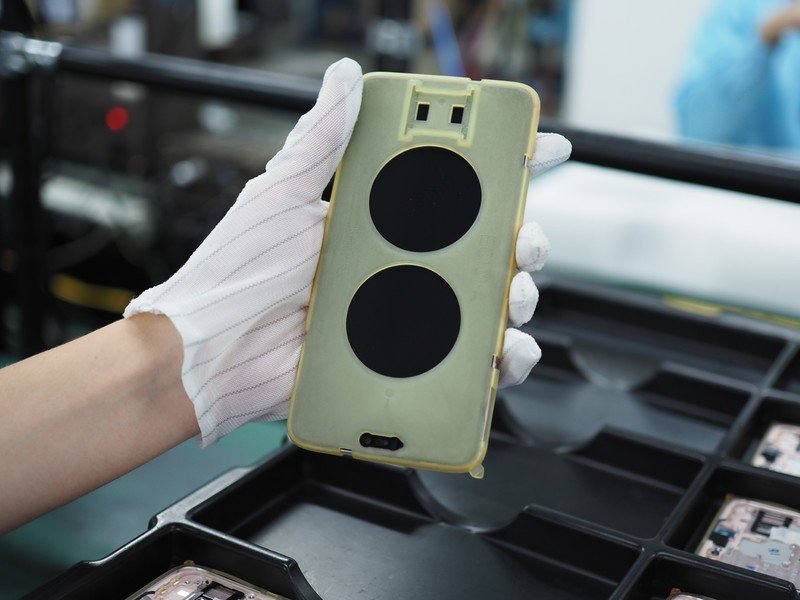
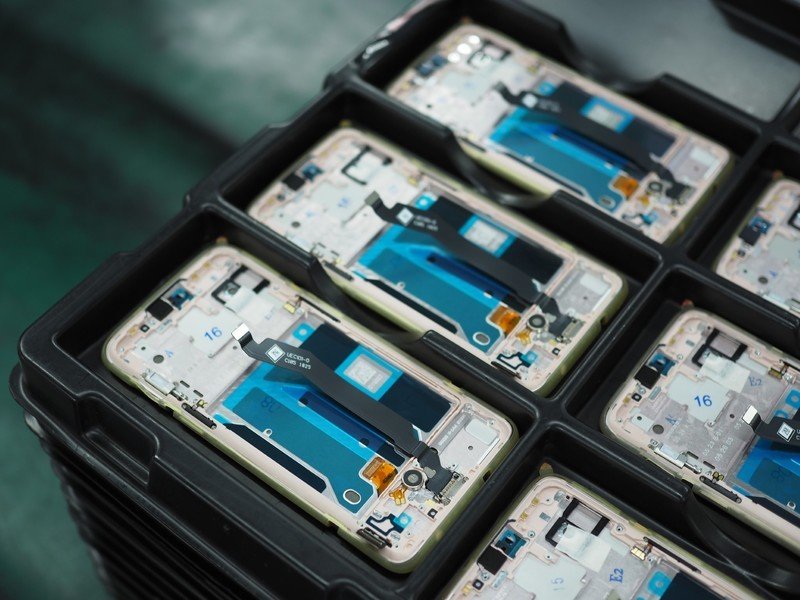
Once that's done, it's time to connect the camera to the mainboard. The camera sensor is removed from its packaging and slotted into the mainboard. The mainboard also contains the Snapdragon 845 chipset, the UFS 2.1 flash memory module, as well as the LPDDR4X RAM along with the Wi-Fi and baseband modems. Essentially, this is the heart of the phone.
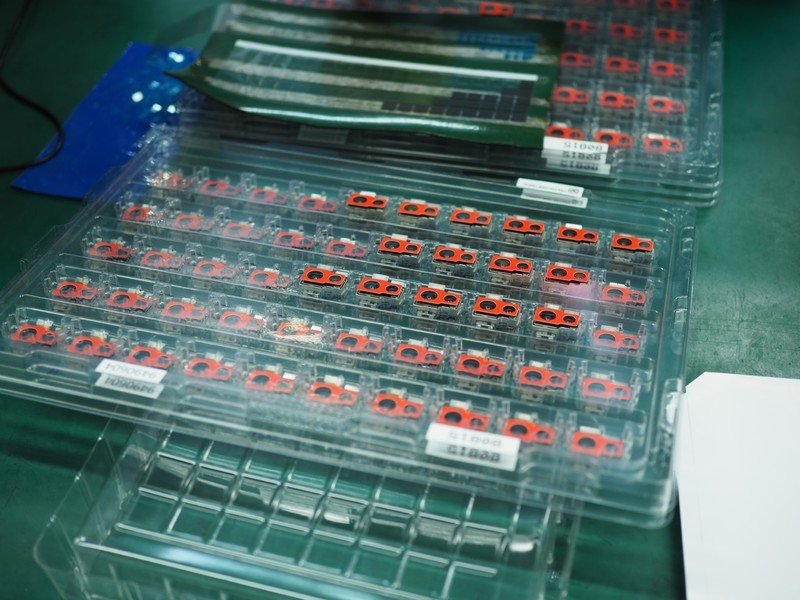
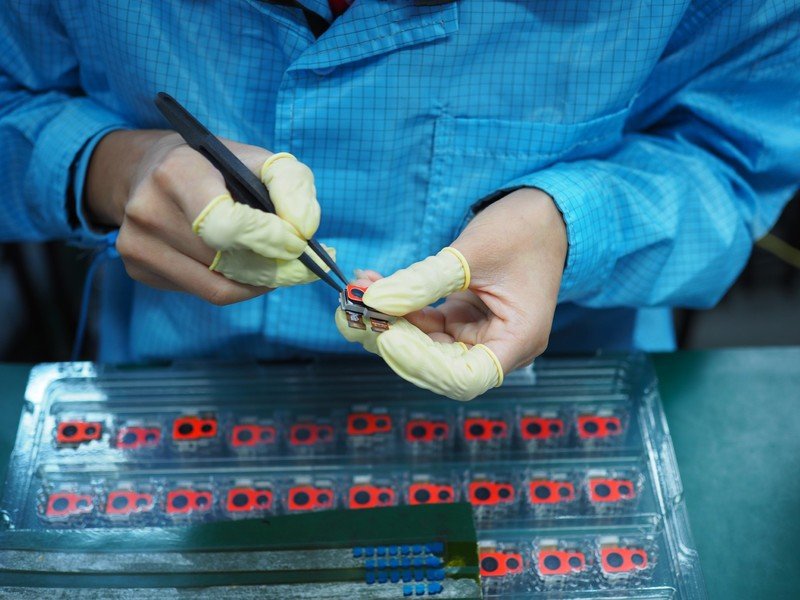
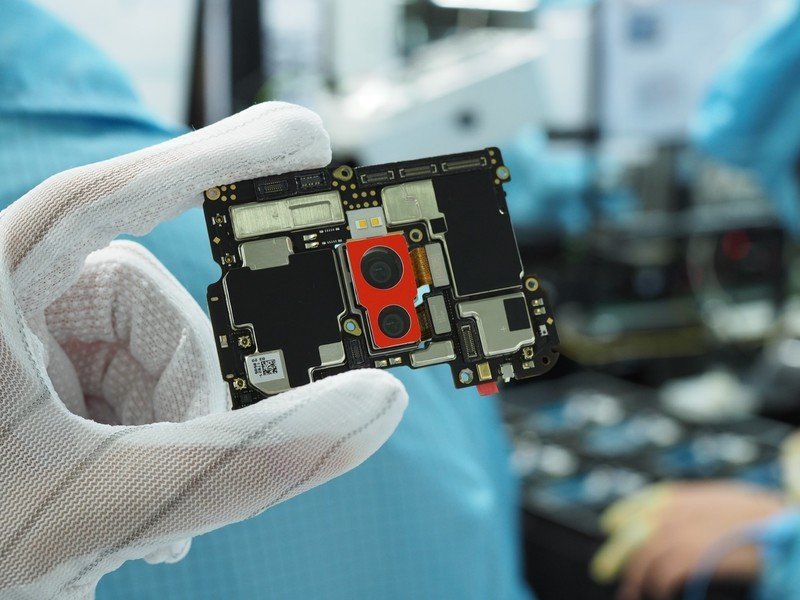
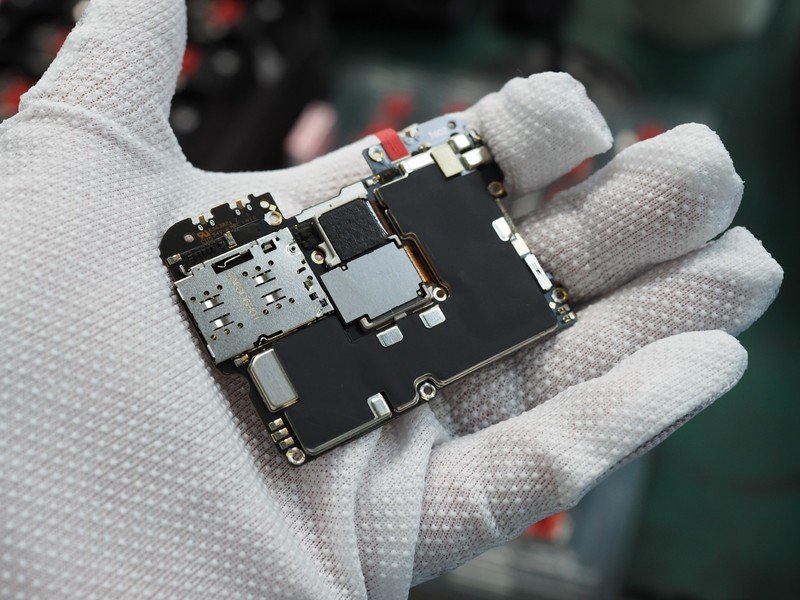
Once the camera module is attached, the mainboard is affixed to the phone, and then the front camera assembly is mounted at the top.
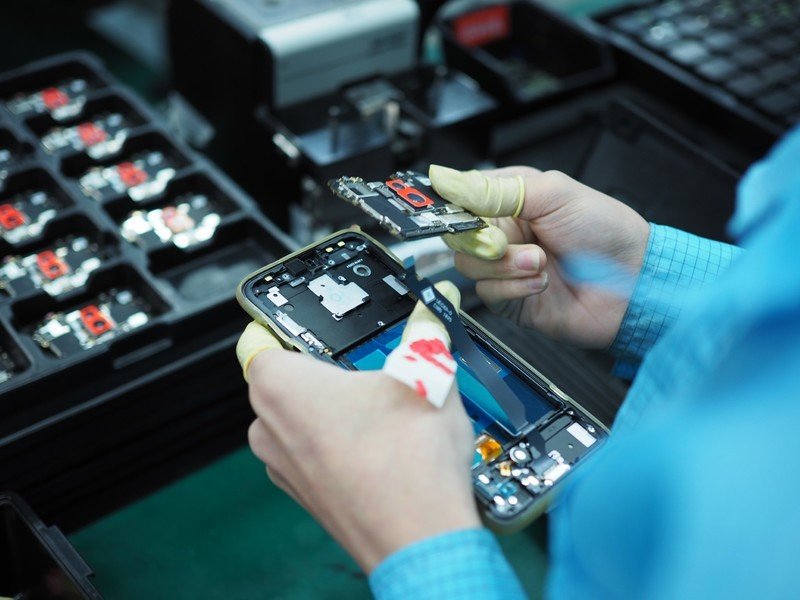
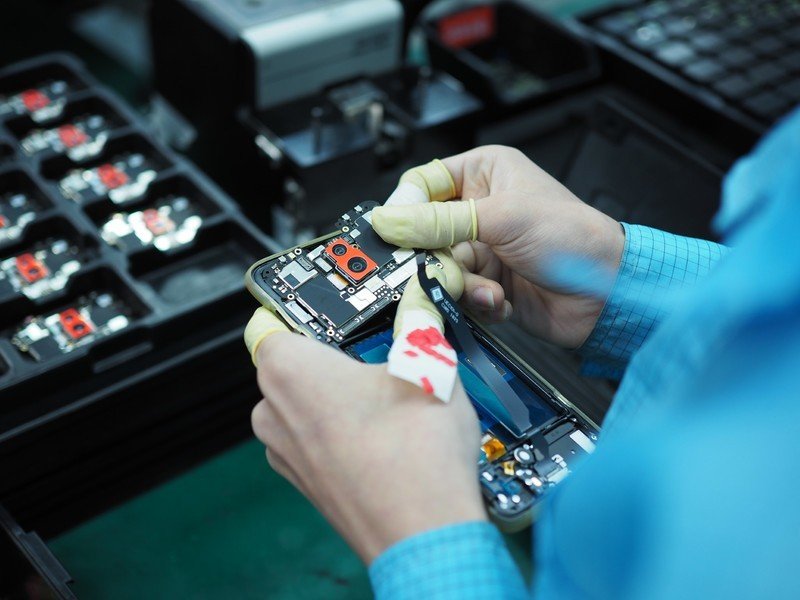
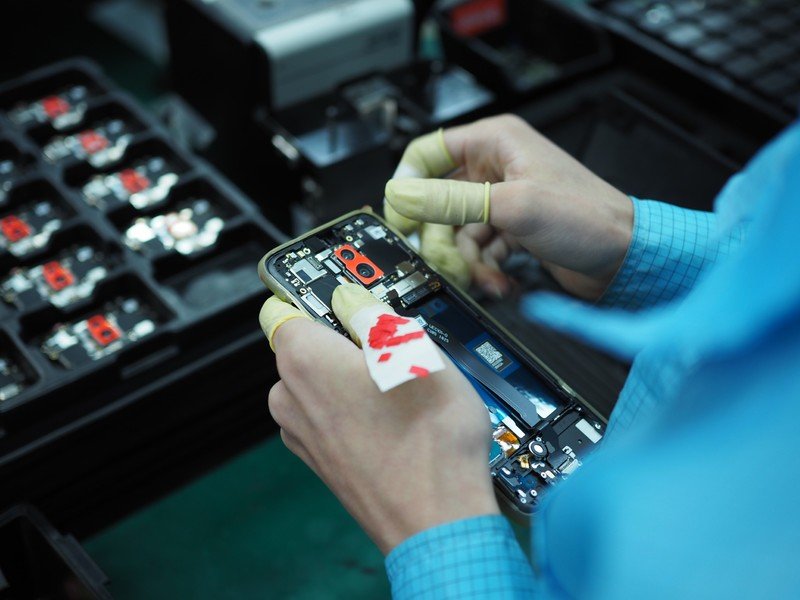
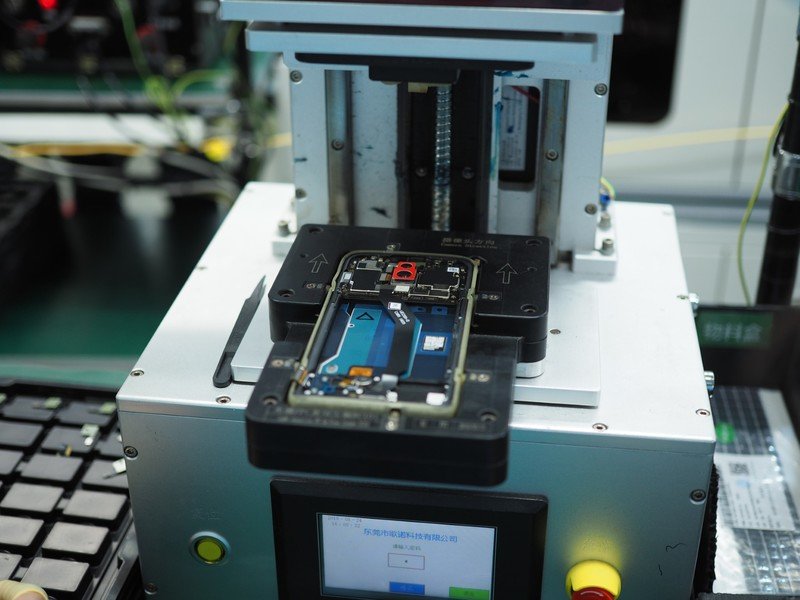
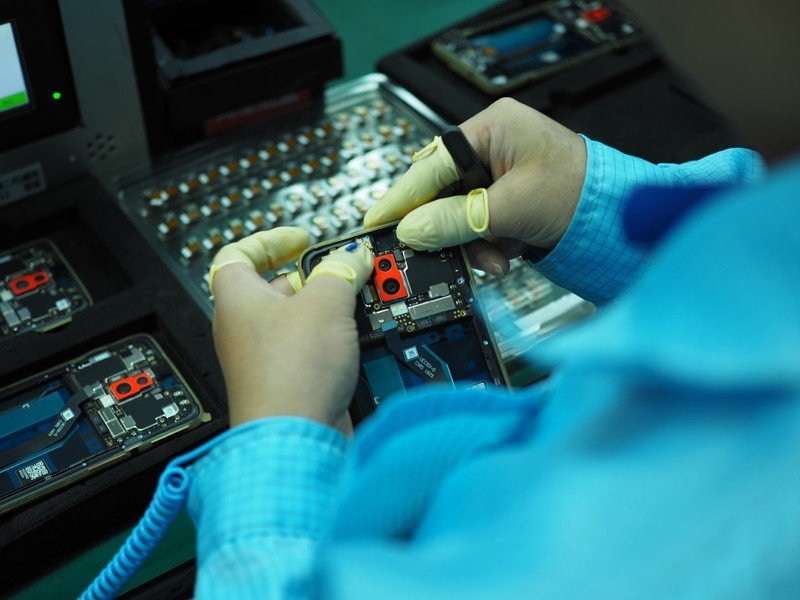
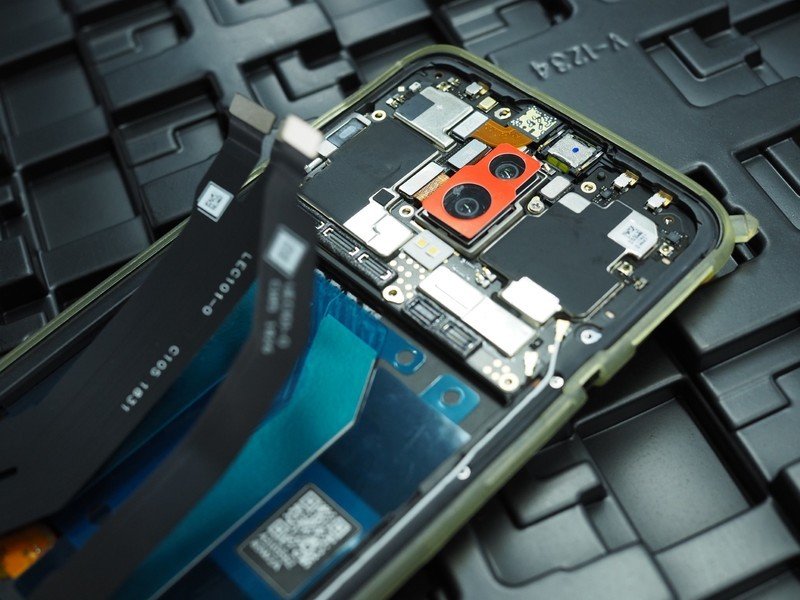
After that, a series of FPC connectors for the screen, 3.5mm jack, and the USB-C port are hooked up to the mainboard.
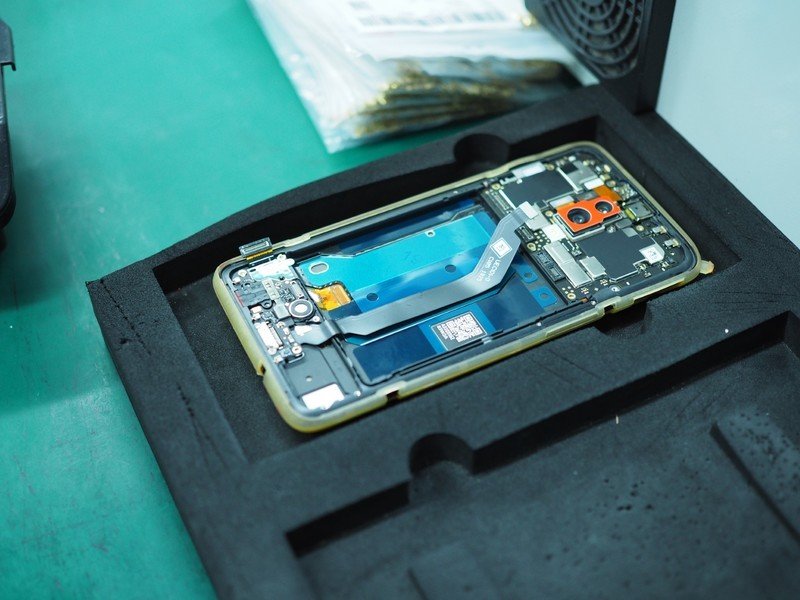
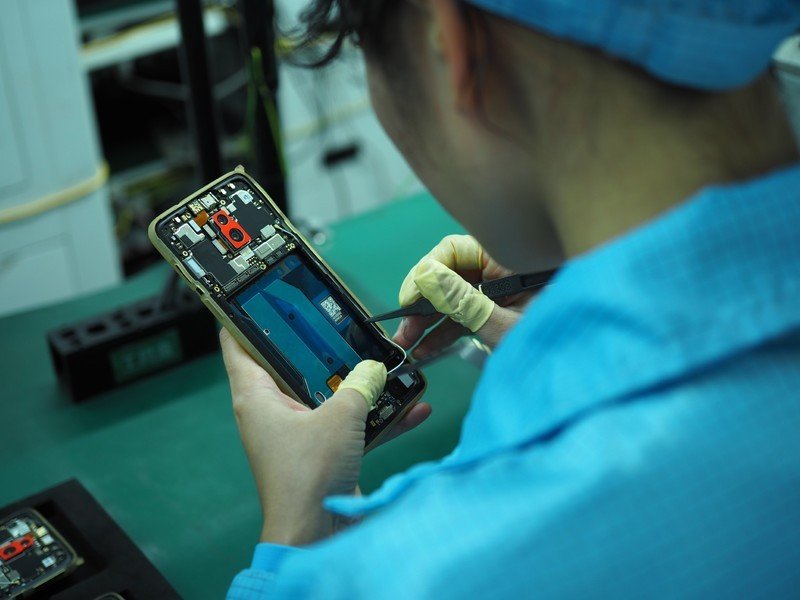
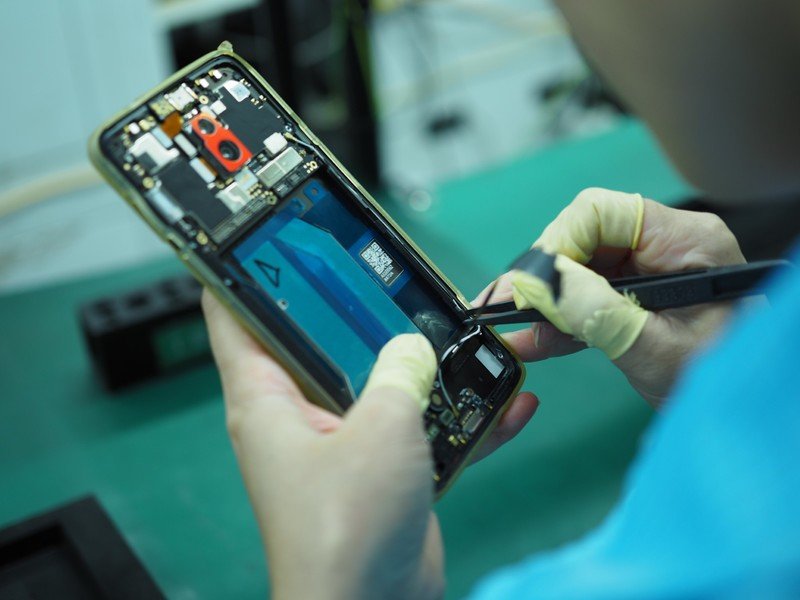
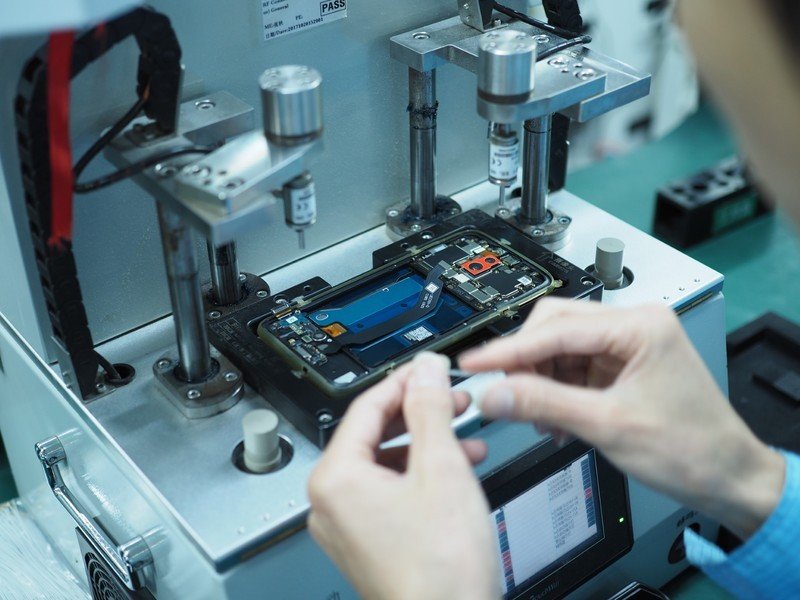
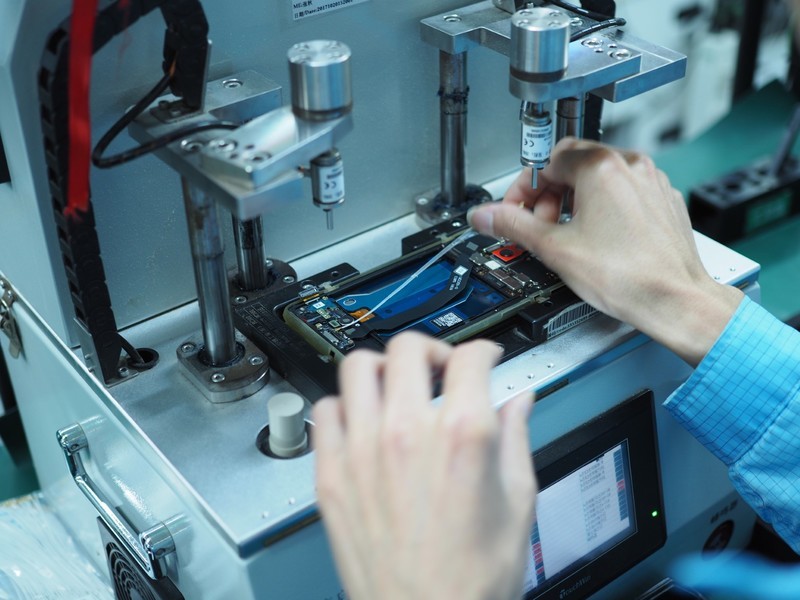
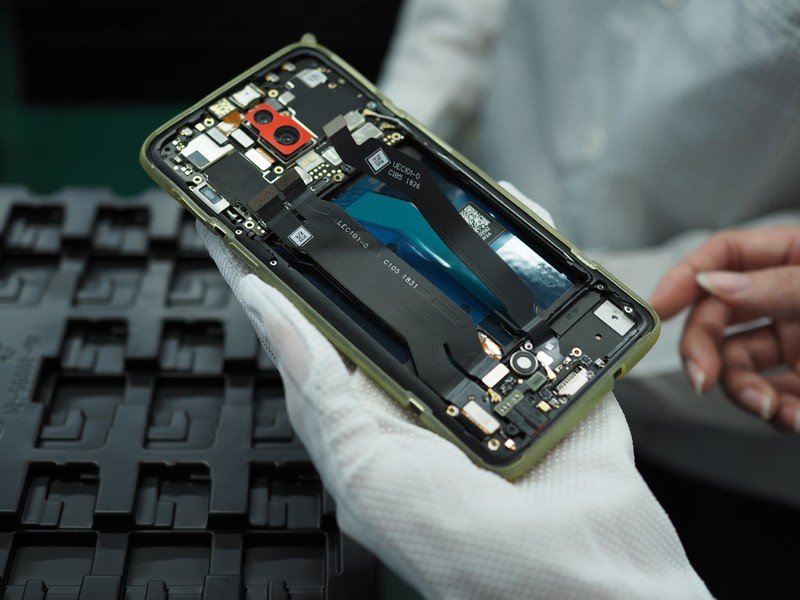
Interestingly, there's a water damage indicator that's located at the bottom. It's essentially a tiny square of paper that is placed on one of the data cables, and it'll turn pink as soon as it comes into contact with any water.

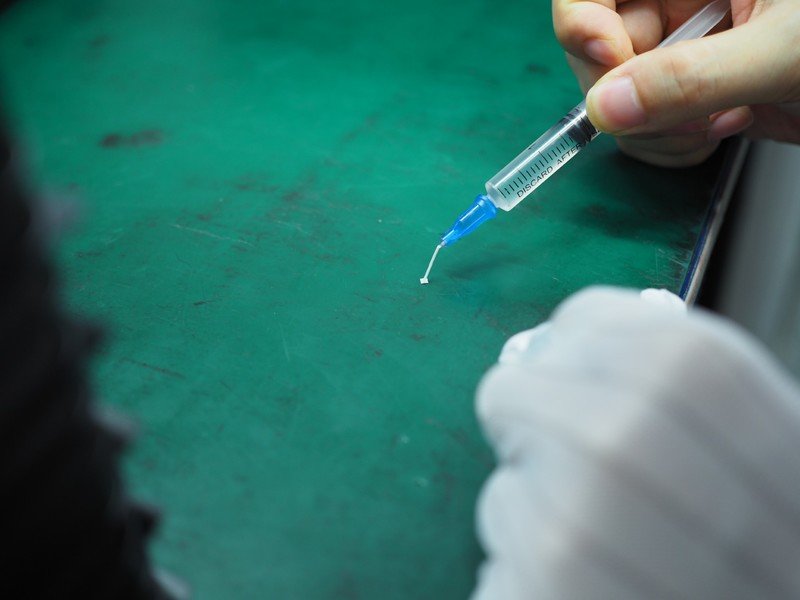
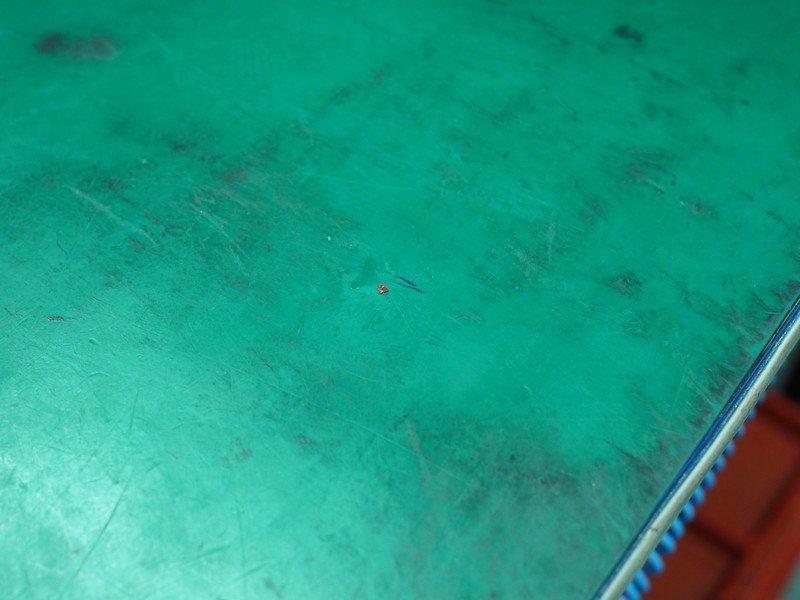
After this, a machine scans the screws and the overall assembly to make sure the tolerances are in order and that there are no defects. Once the parts are assembled, the plastic antenna frame is added to the top section, and a similar housing over the bottom section covering the USB-C port and the 3.5mm jack.
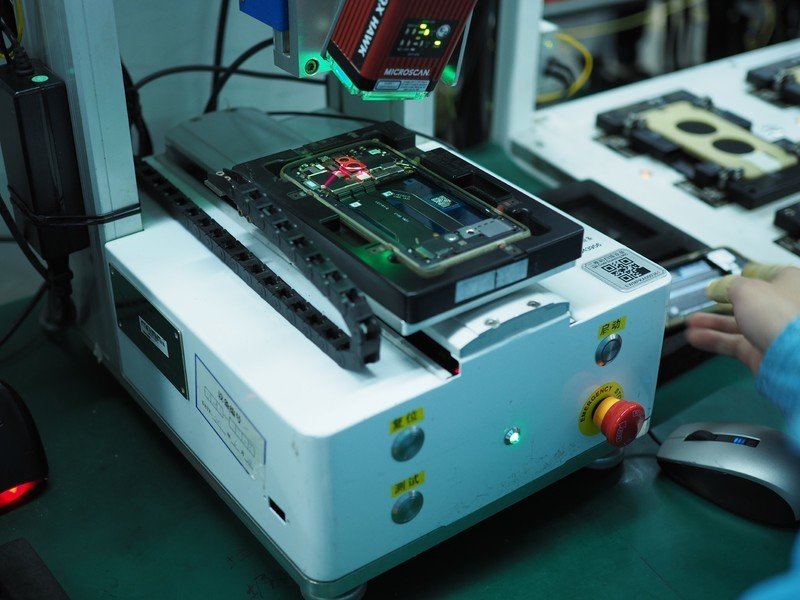
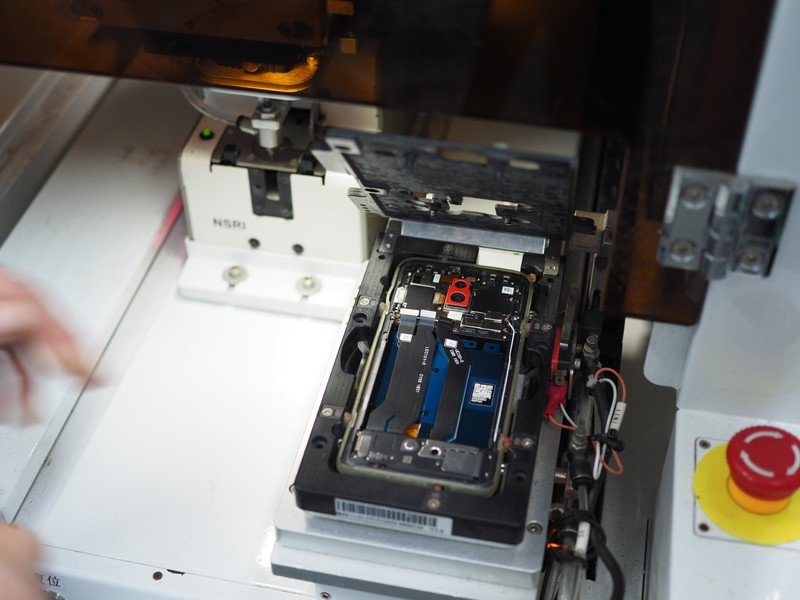
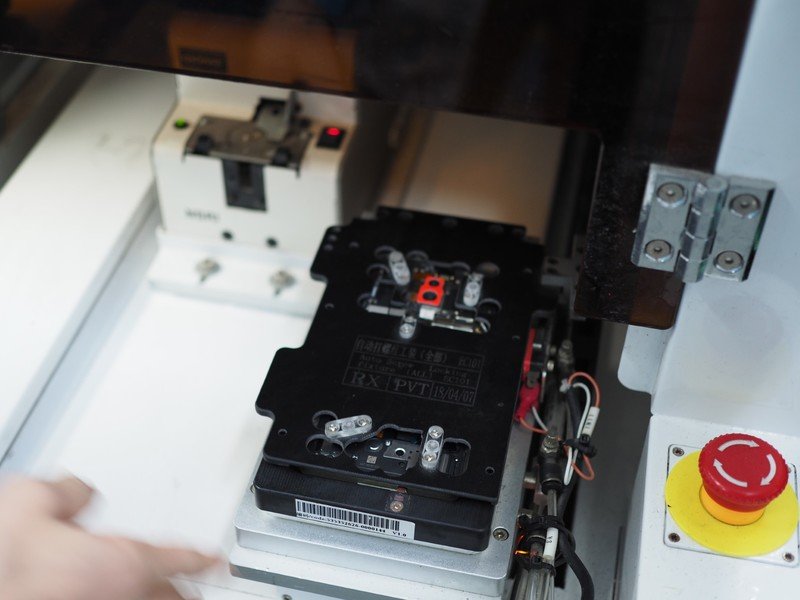
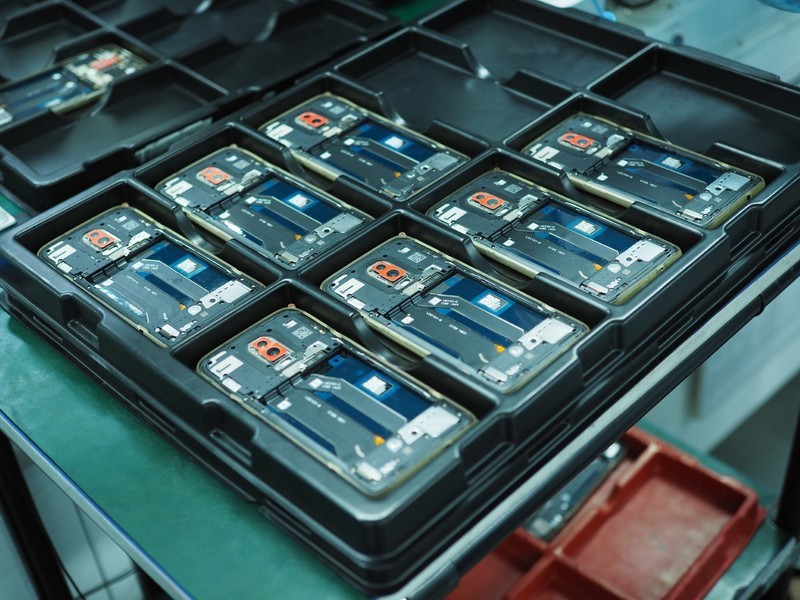
That marks the end of the assembly, and now it's time to slot in the battery. This is fairly straightforward, and the 3300mAh battery has a green pull tab that makes it easy to remove (even though it isn't easily accessible as you'll have to remove the glass back to get to it).
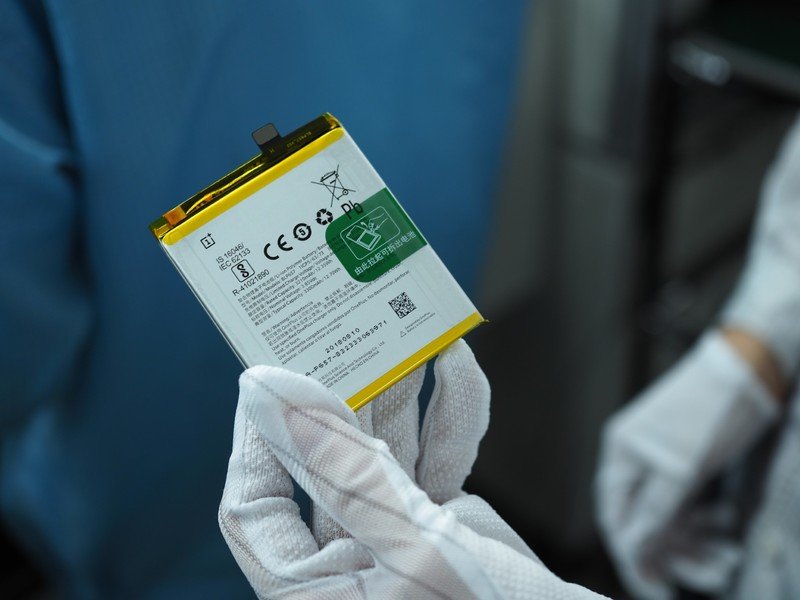
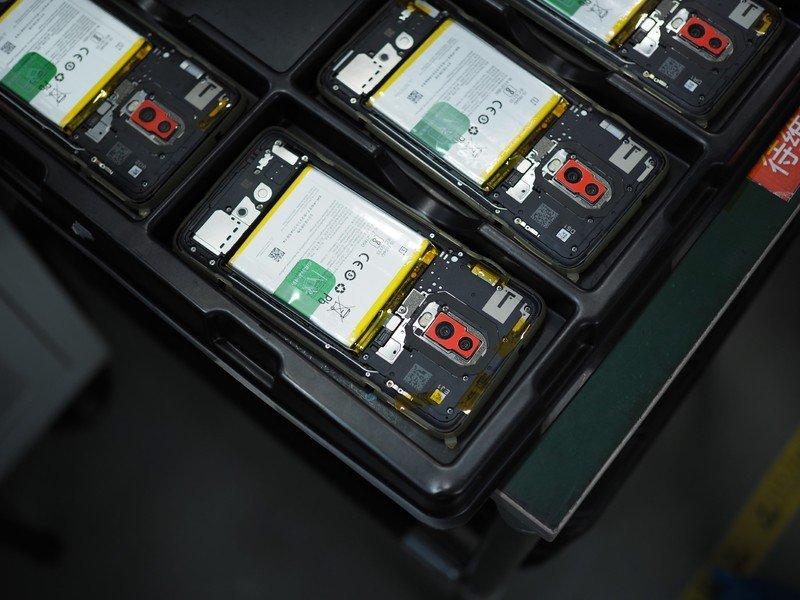
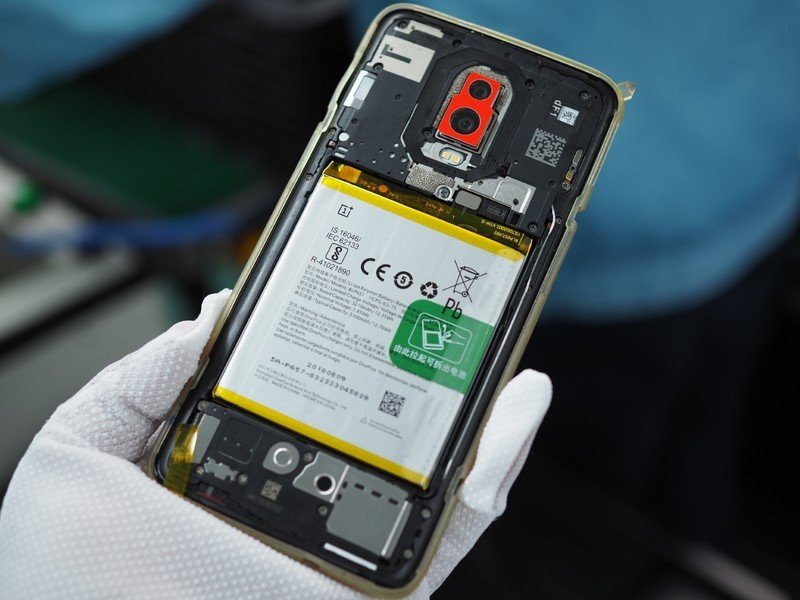
The glass itself is manufactured at a third-party supplier, and the first step is to affix the fingerprint sensor cable to the back. That's the long orange cable you see in the image above. Once the cable for the fingerprint sensor is affixed, it's time to attach the lens cover over the camera housing.
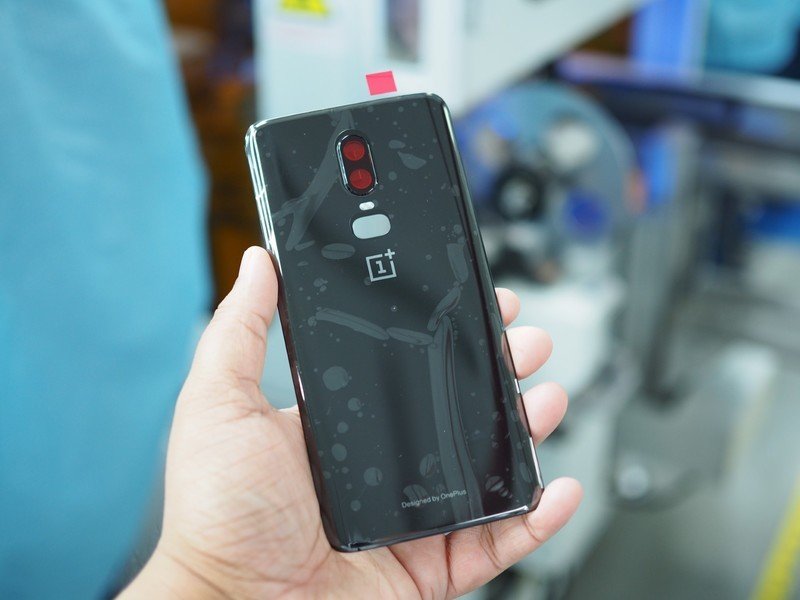
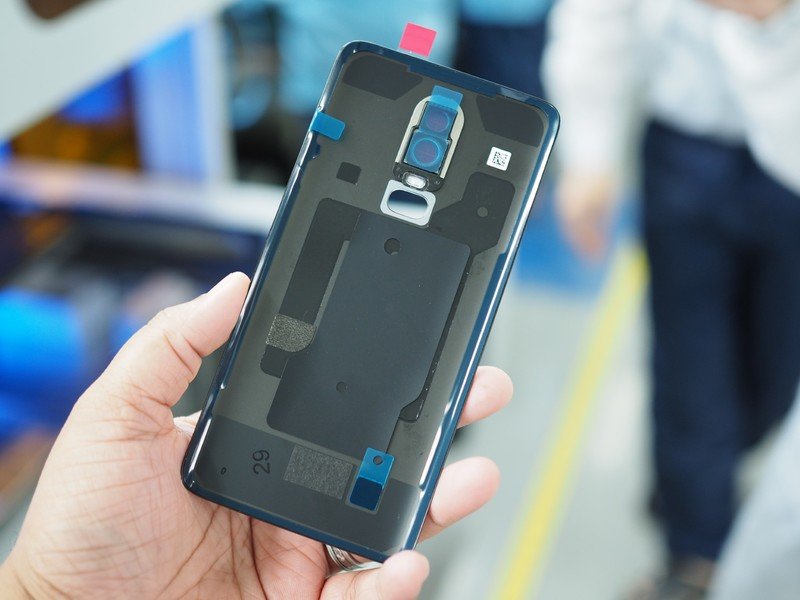
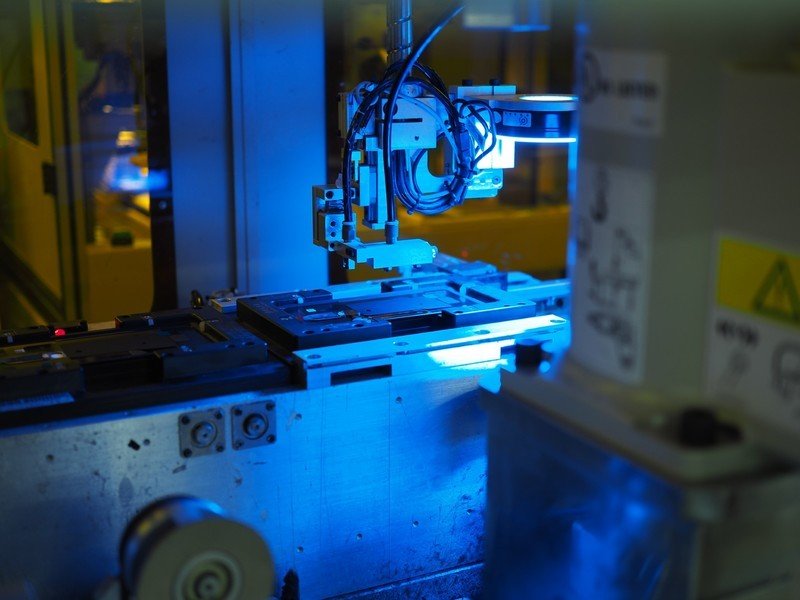
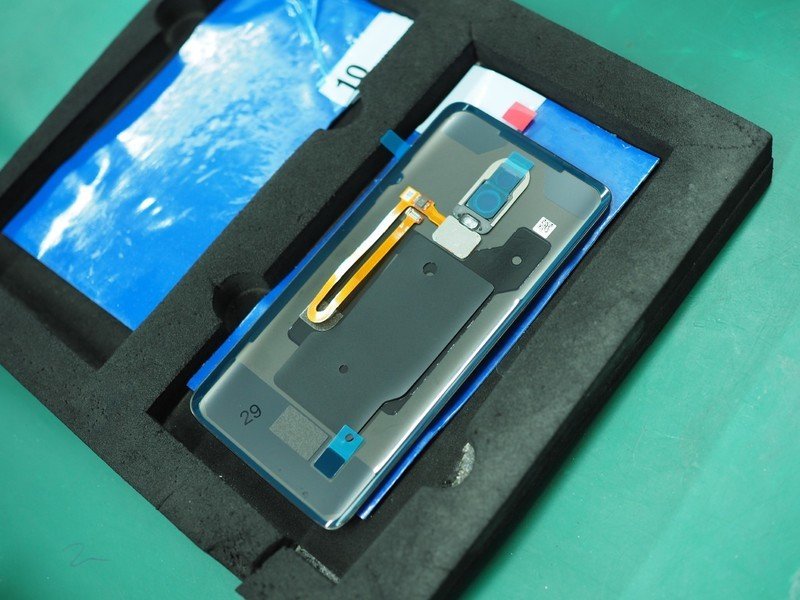
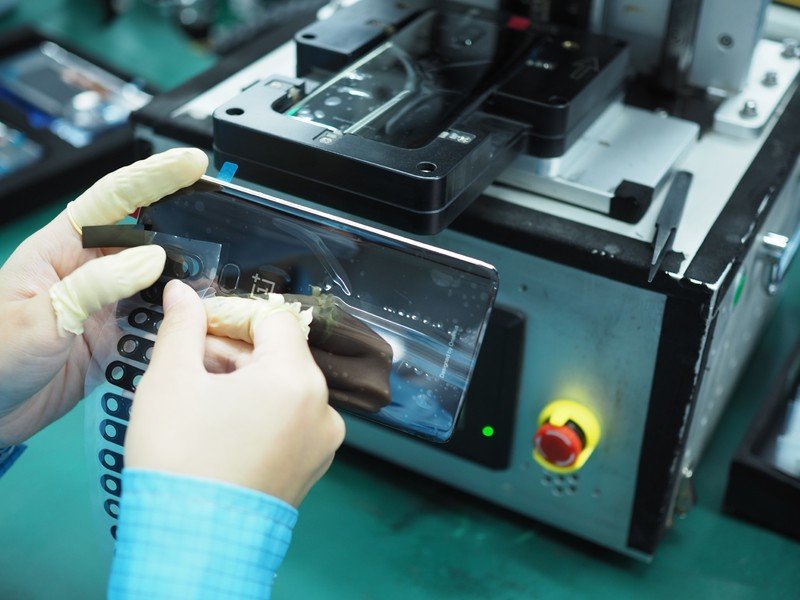
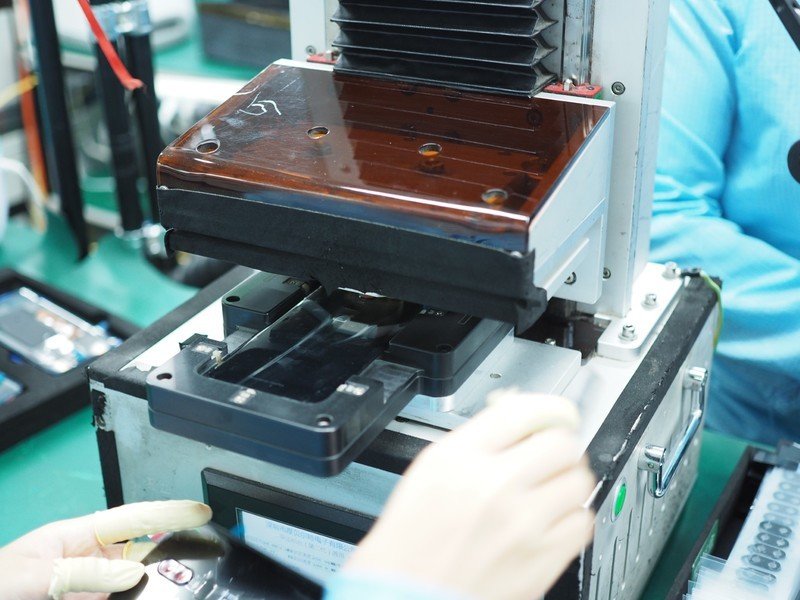
Now comes the interesting part — attaching the glass back to the phone. A machine stamps the glass back into place, and another machine rolls the sides so the adhesive is firmly affixed.
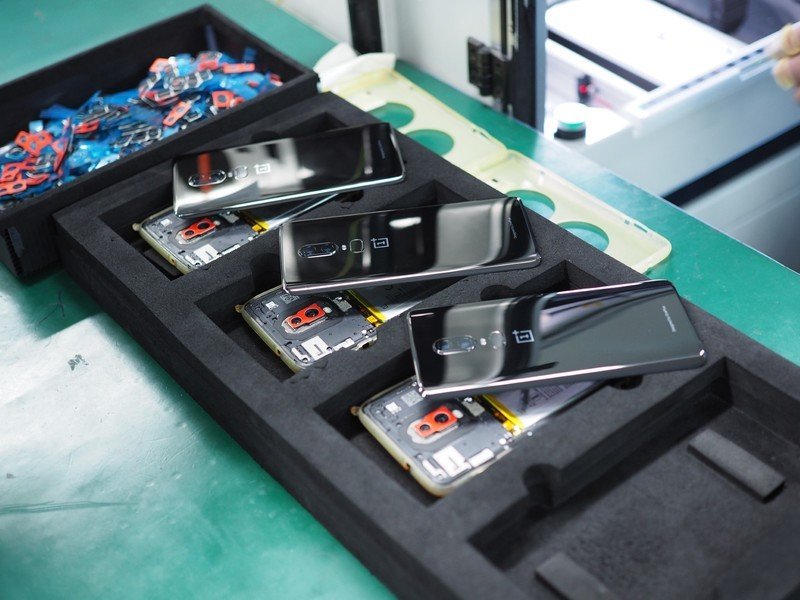
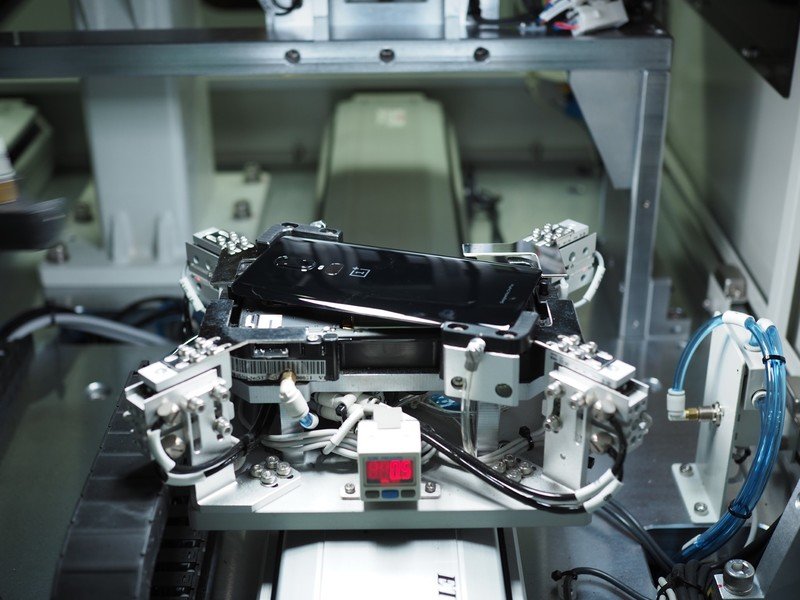
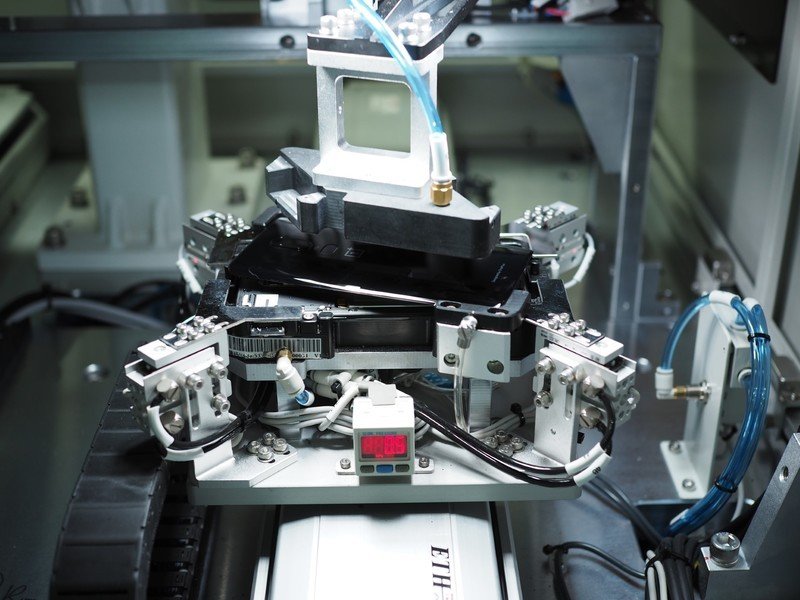
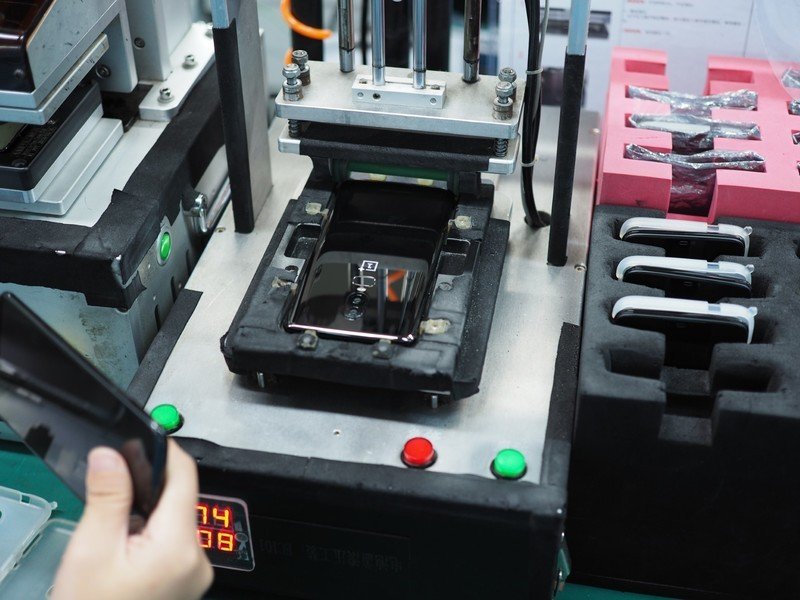
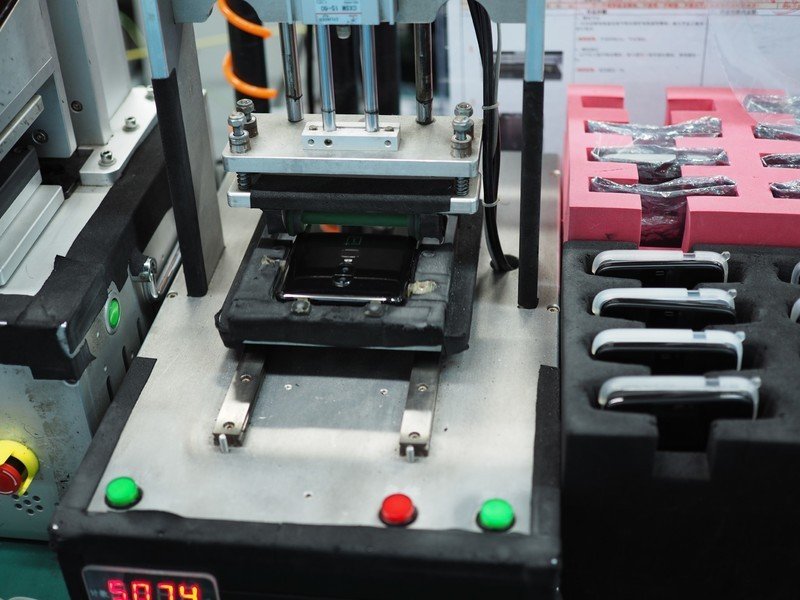
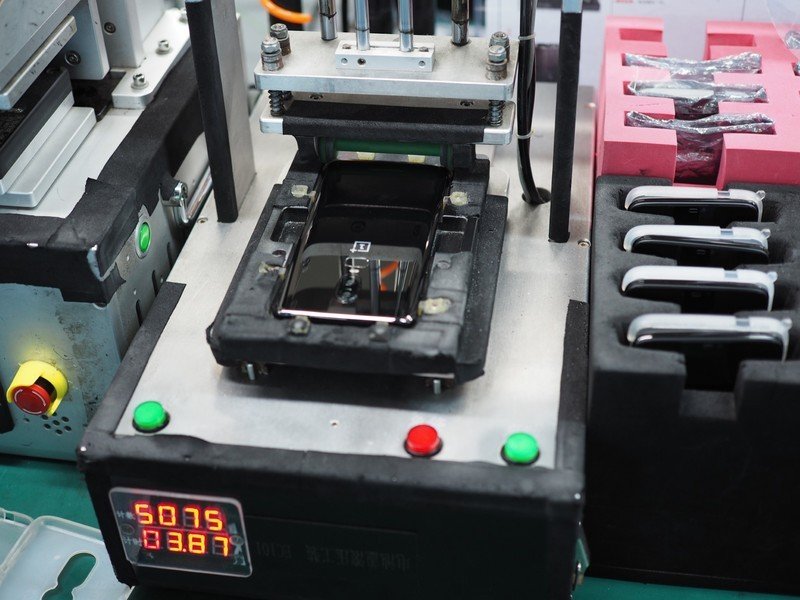
Once the final assembly is done, it's time for testing the phone. A battery of tests are conducted on the assembly floor itself — including battery charging tests, display and color accuracy tests, as well as vibration and camera sensor focusing tests.
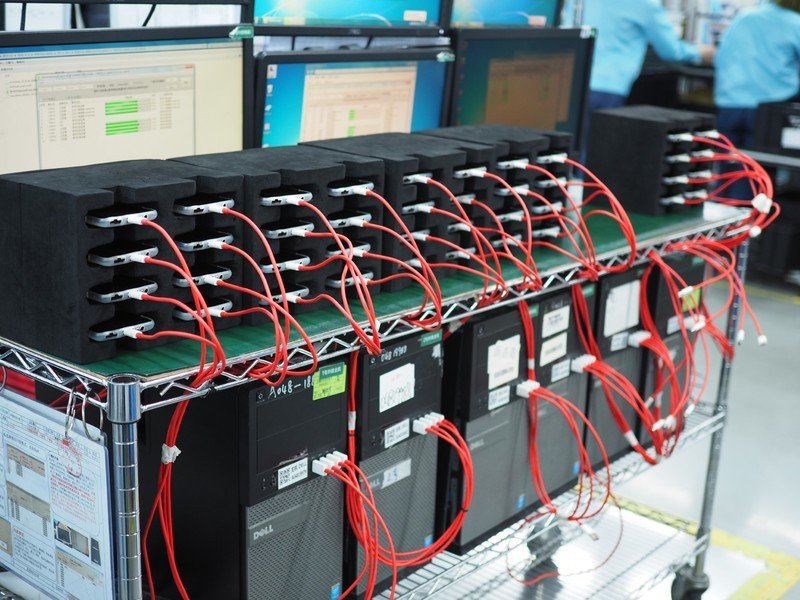
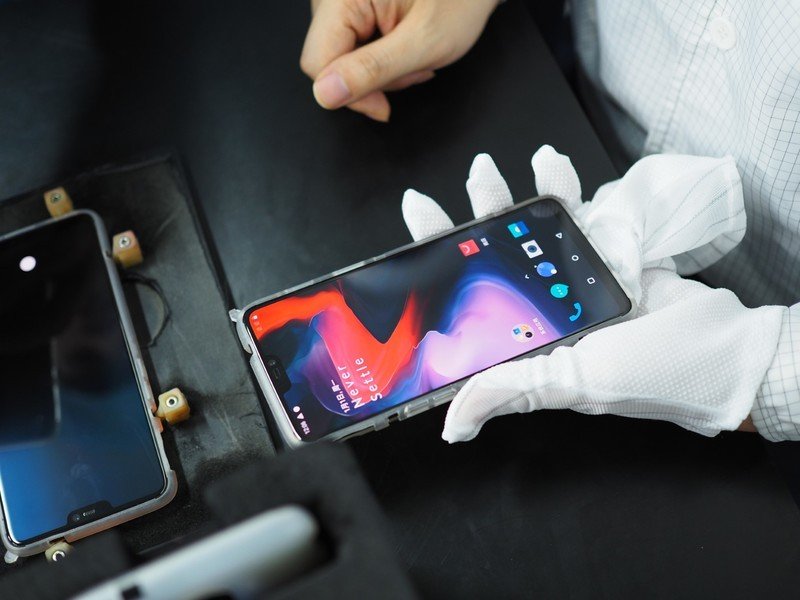
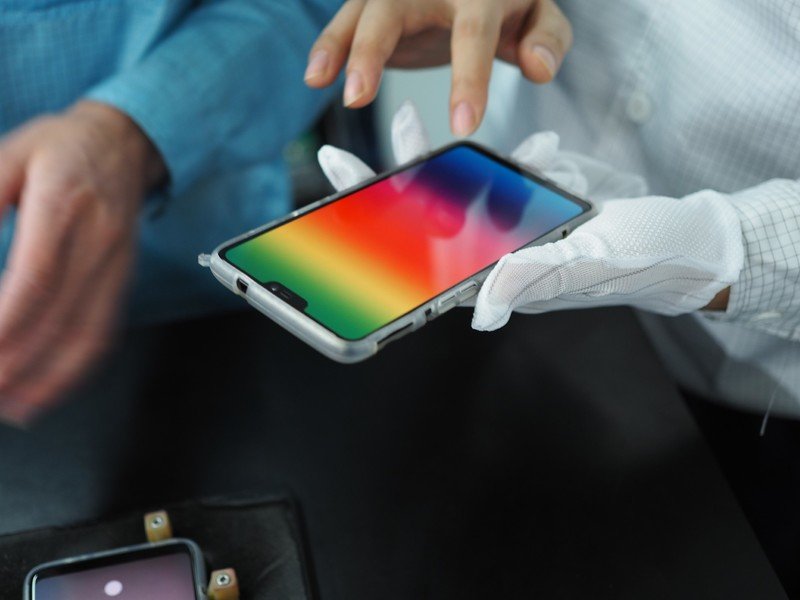
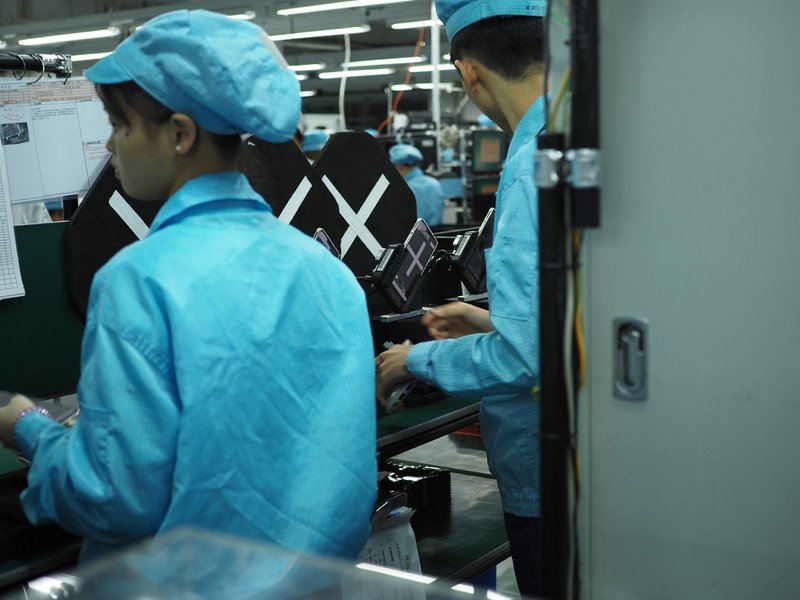
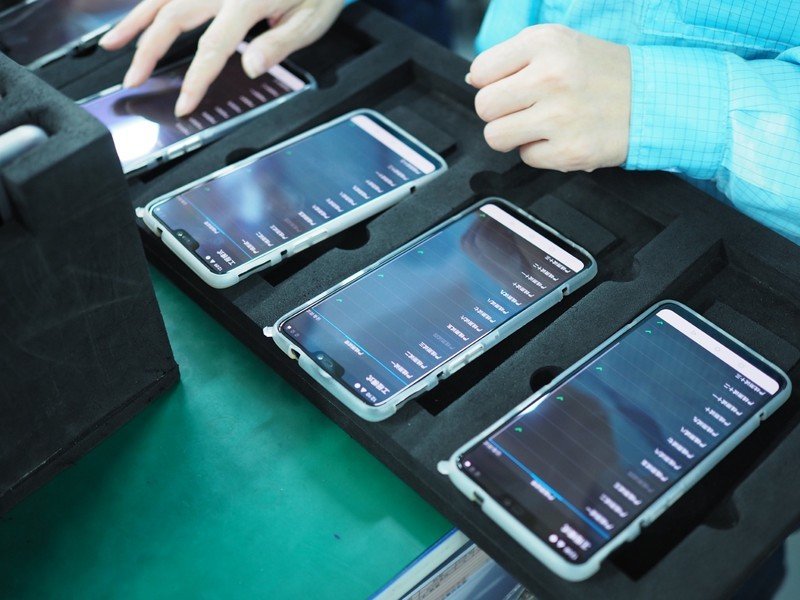
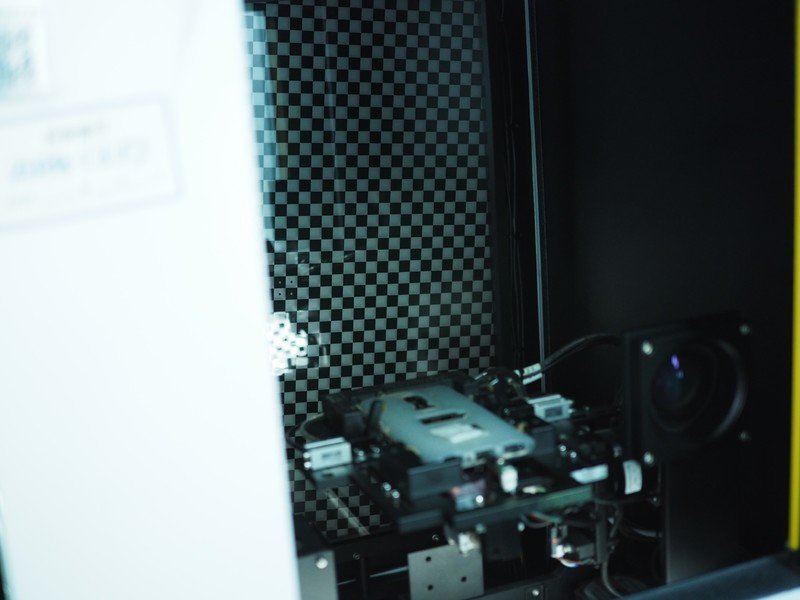
Once the tests are done, a layer of film is fixed over the entire surface of the phone, and then it's off to packaging. I always assumed the labels on the back of the box were done by a robot and not by hand, so it was surprising to find that this isn't the case.
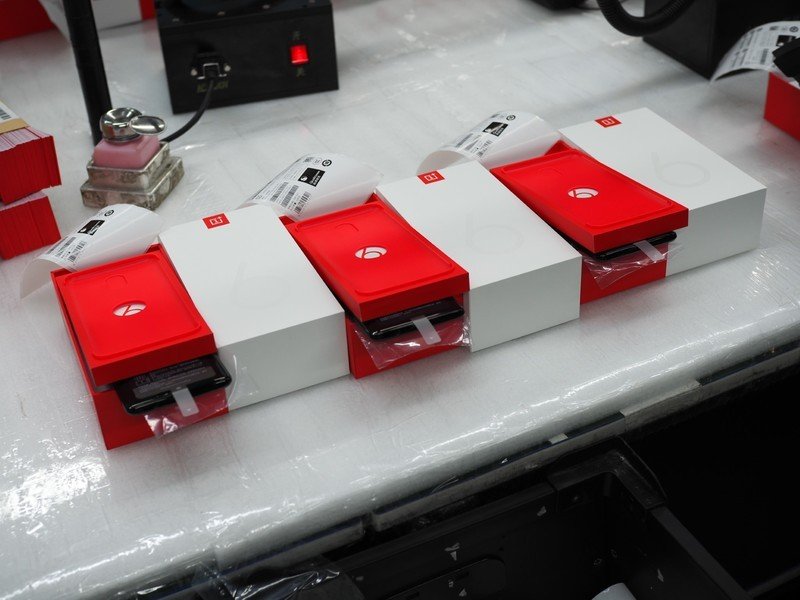
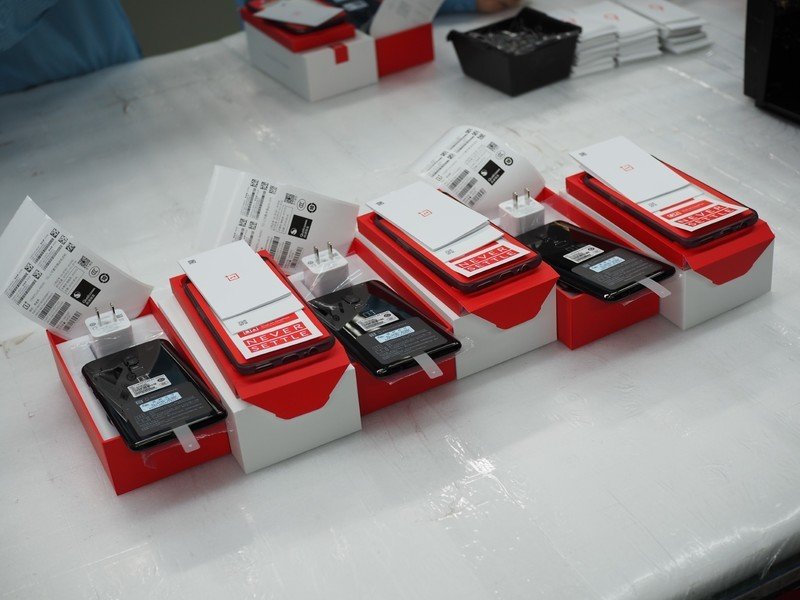
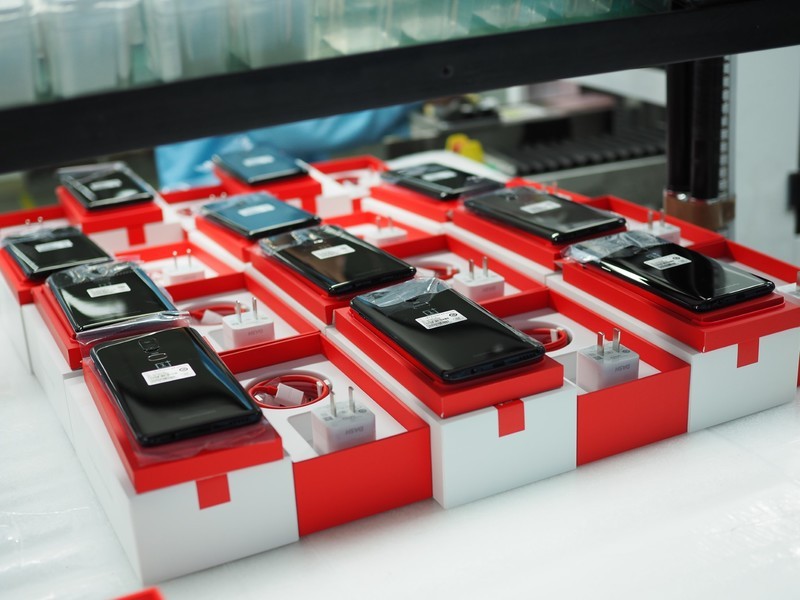
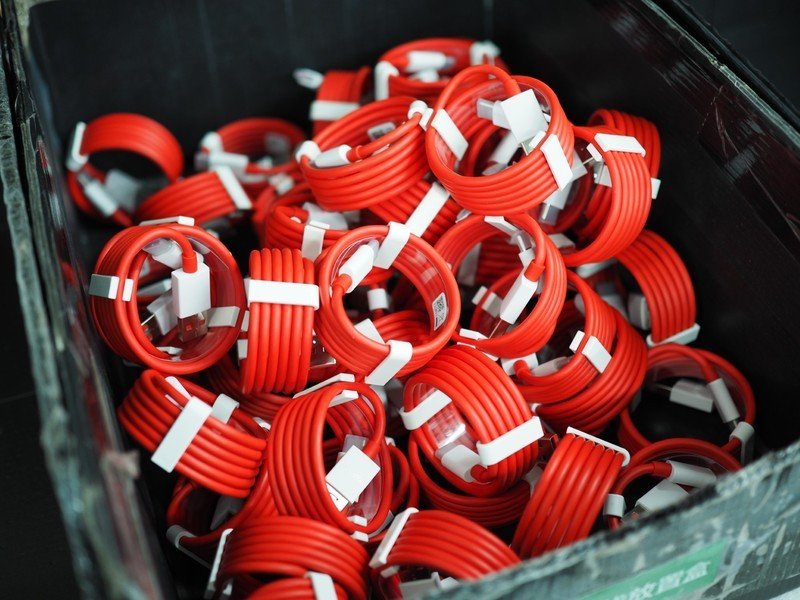
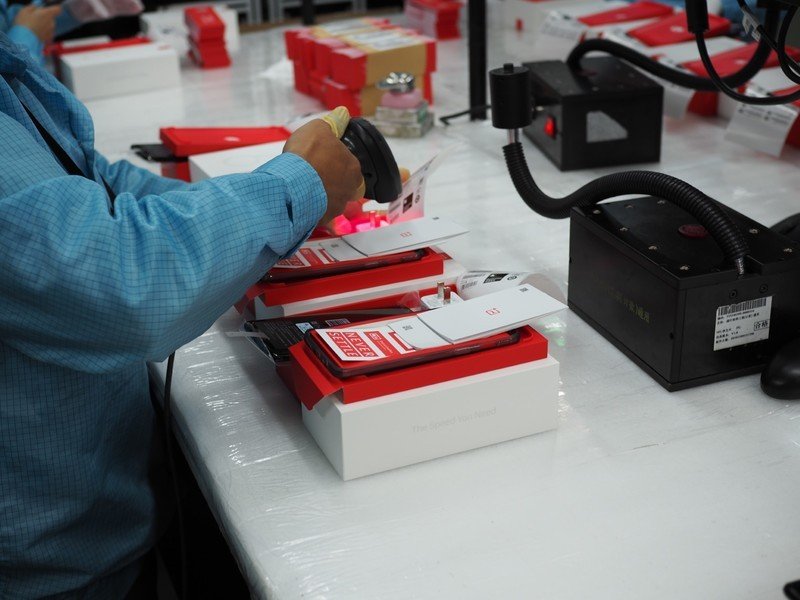
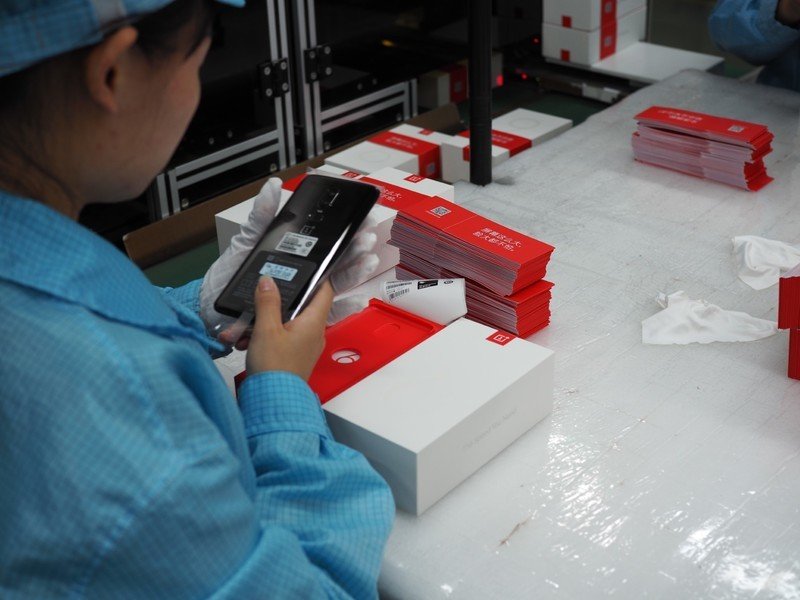
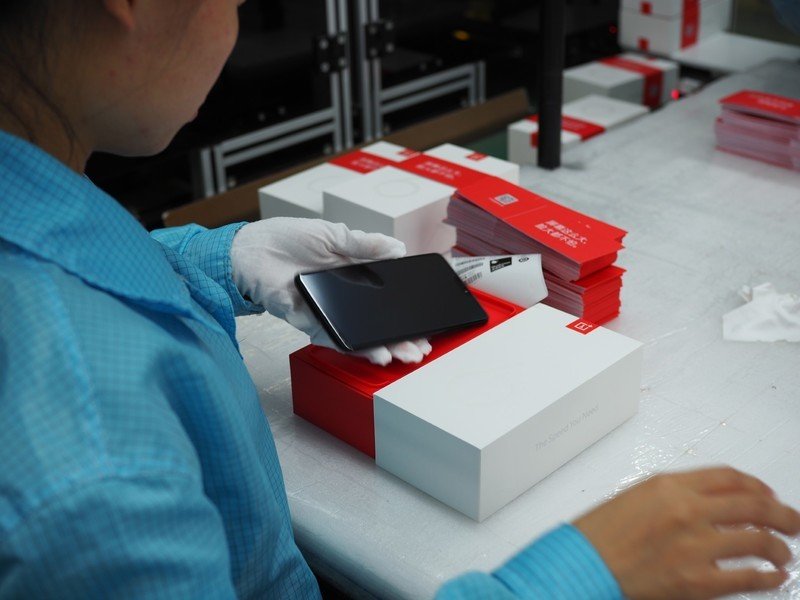
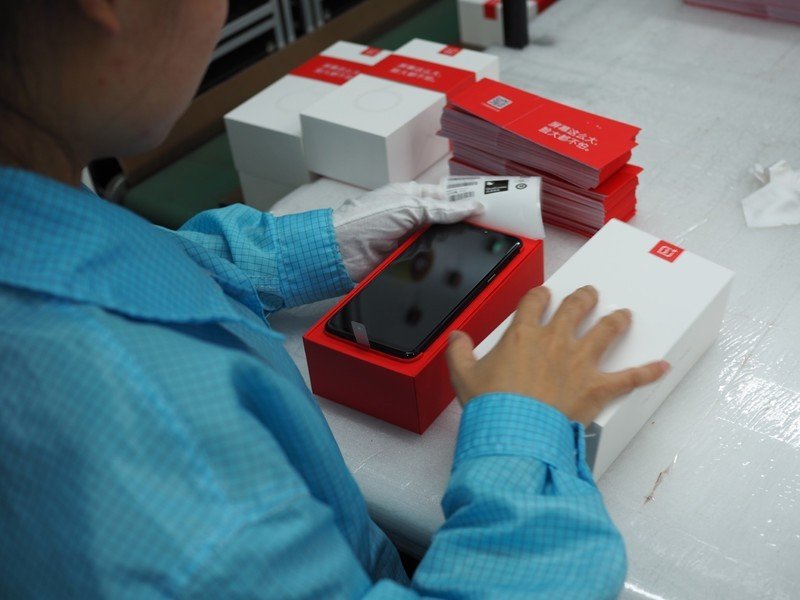
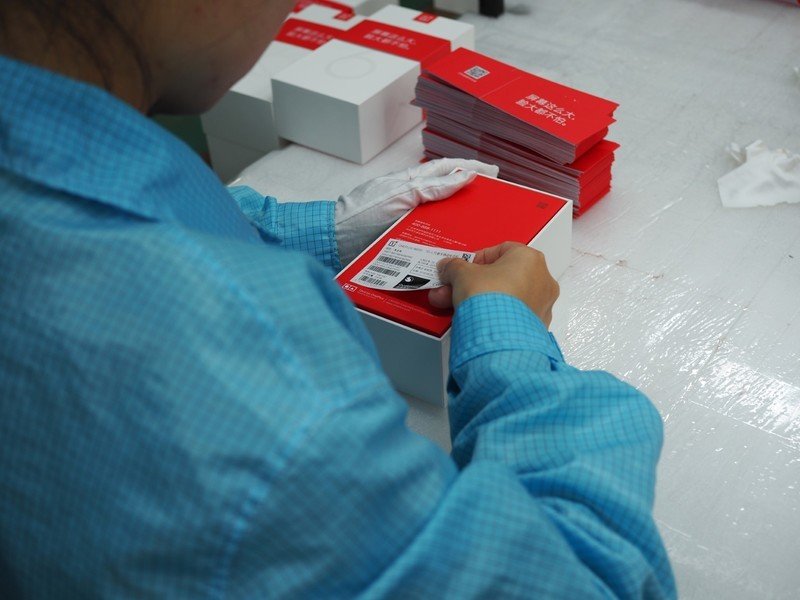
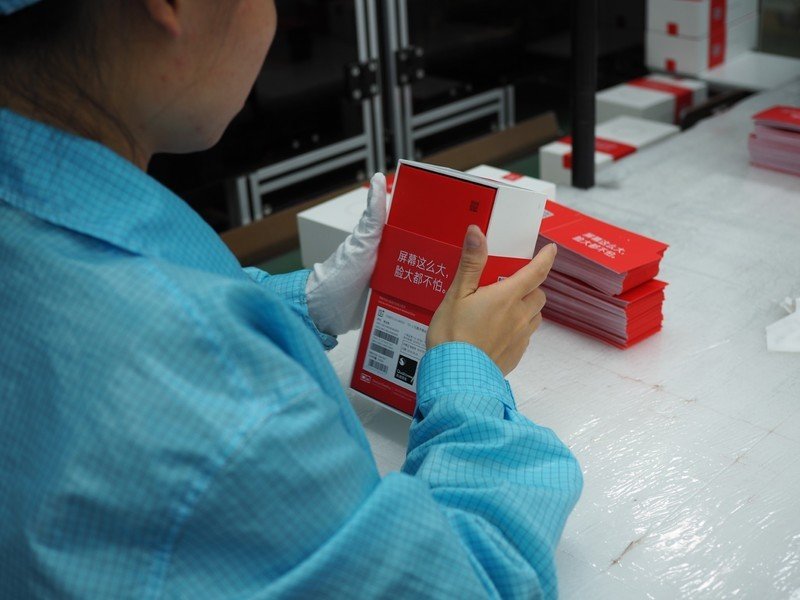
Once the packaging is done, the OnePlus 6 is ready to be put into containers and sent off to various destinations around the globe. The assembly line I went to primarily caters to the Chinese market, as you can make out from the product packaging.
It's very interesting to see how phones are put together, even more so when you consider the sheer amount of tech that goes into such a small package. Similarly, the scale at which these devices are manufactured is mind-boggling, particularly in a city like Shenzhen. It's been called the Silicon Valley of hardware, and that label fits once you see just how much of the world's gadgets are made here.
It's no coincidence that OnePlus decided to have its global headquarters in Shenzhen — easy access to manufacturing facilities allows the company to go through several iterations of a design in a matter of weeks. That design prowess is immediately evident once you start using the OnePlus 6: the phone feels just as premium as "true" flagships that cost north of $1,000.
I sat down with OnePlus CEO Pete Lau to talk about how the company approaches product design and the challenges it faces in the handset segment, so stay tuned for that next week.
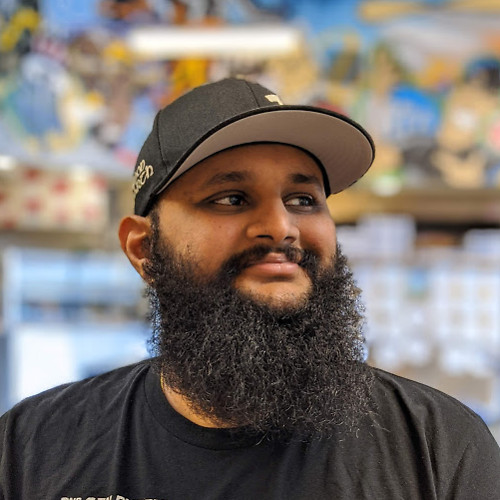
Harish Jonnalagadda is Android Central's Senior Editor overseeing mobile coverage. In his current role, he leads the site's coverage of Chinese phone brands, networking products, and AV gear. He has been testing phones for over a decade, and has extensive experience in mobile hardware and the global semiconductor industry. Contact him on Twitter at @chunkynerd.