Made in Taiwan: How HTC designs, manufactures and tests its new U11 flagship
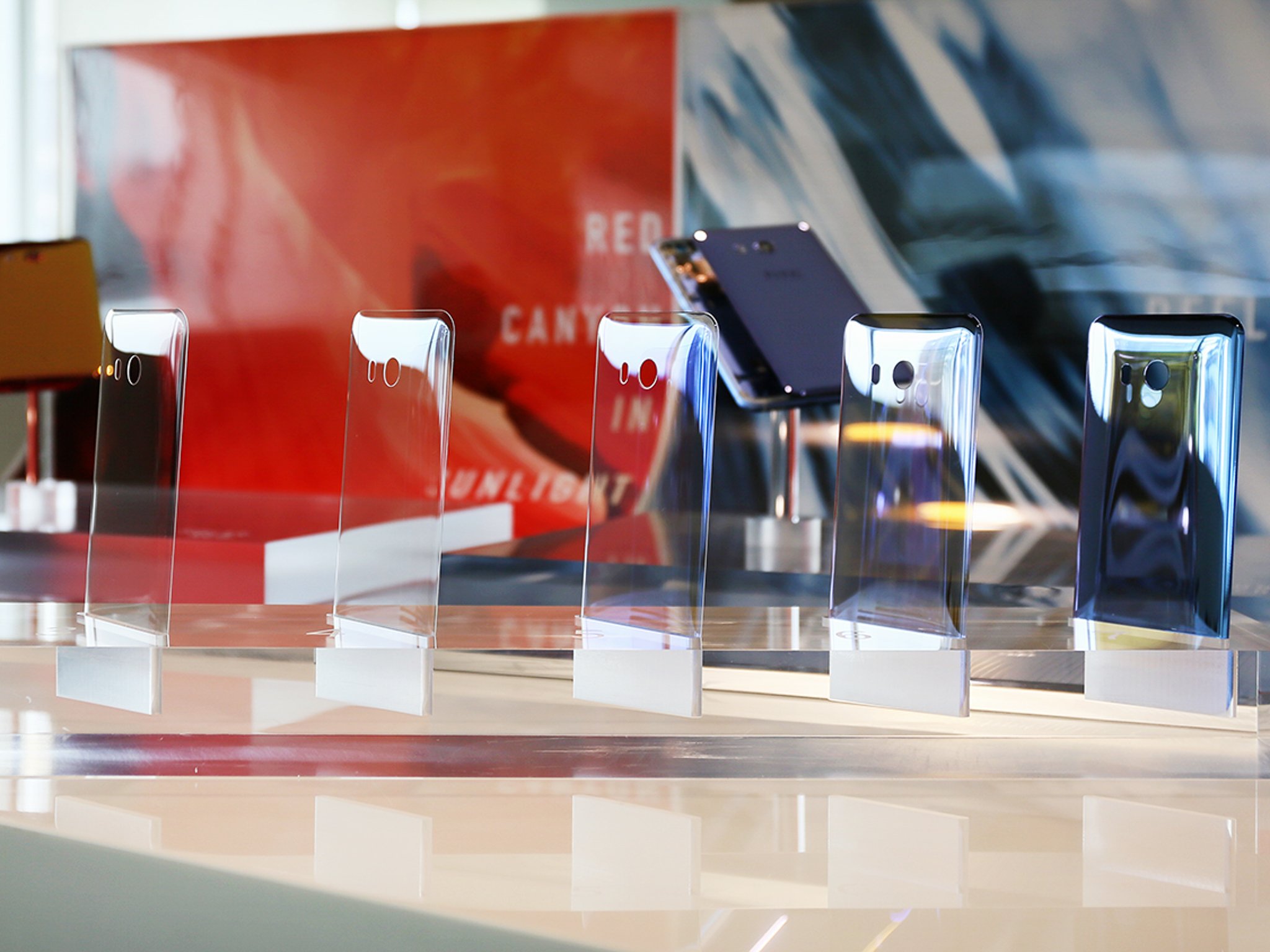
Leading up to the launch of the HTC U11, the company opened up its doors to show the amazing process that goes into making each flagship. I was lucky enough to be one of the journalists invited to see how it all comes together in Taipei, Taiwan. Through several buildings, offices, labs and production lines, I saw how HTC took the U11 from the early stages of design all the way to testing of individual components and finally assembly of individual phones that will soon be on store shelves.
From start to finish, it was an incredibly insightful experience.
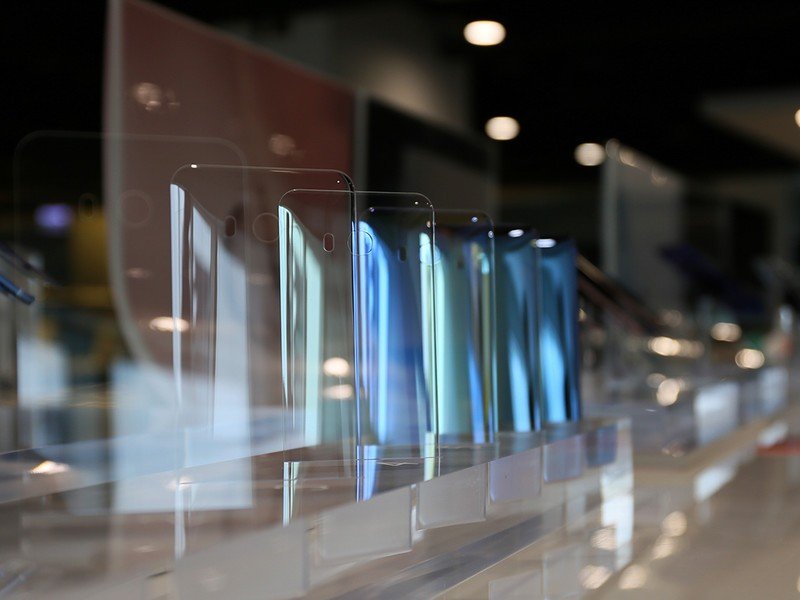
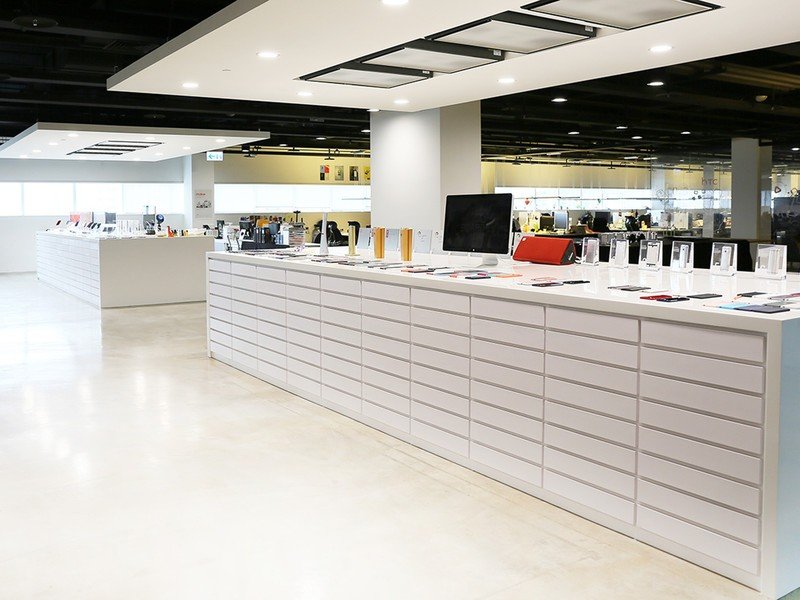
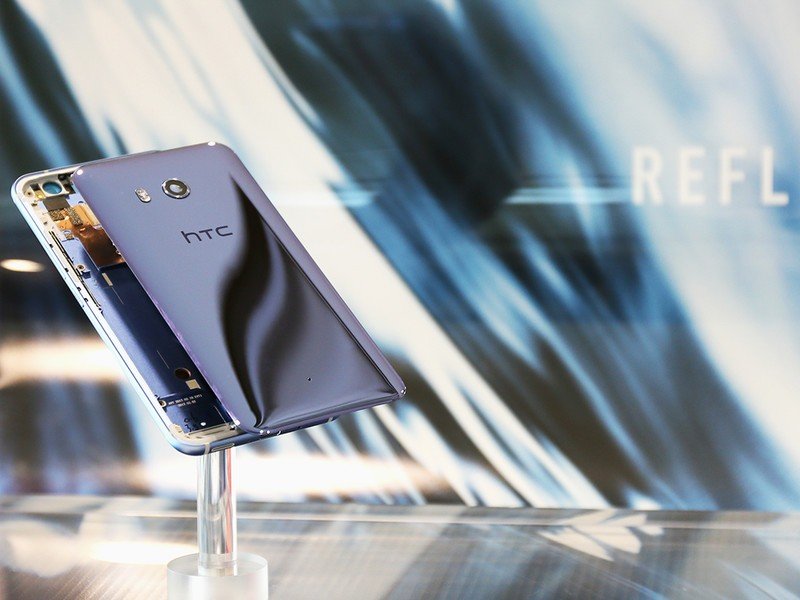
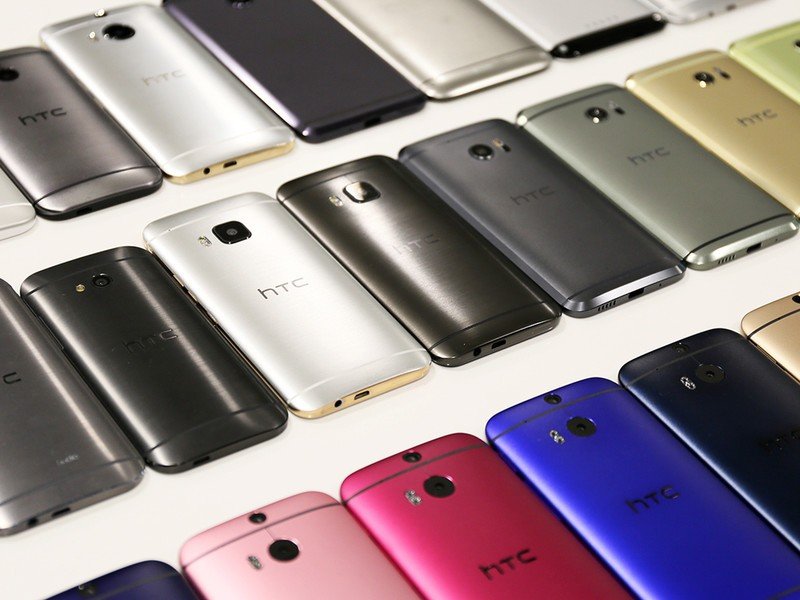
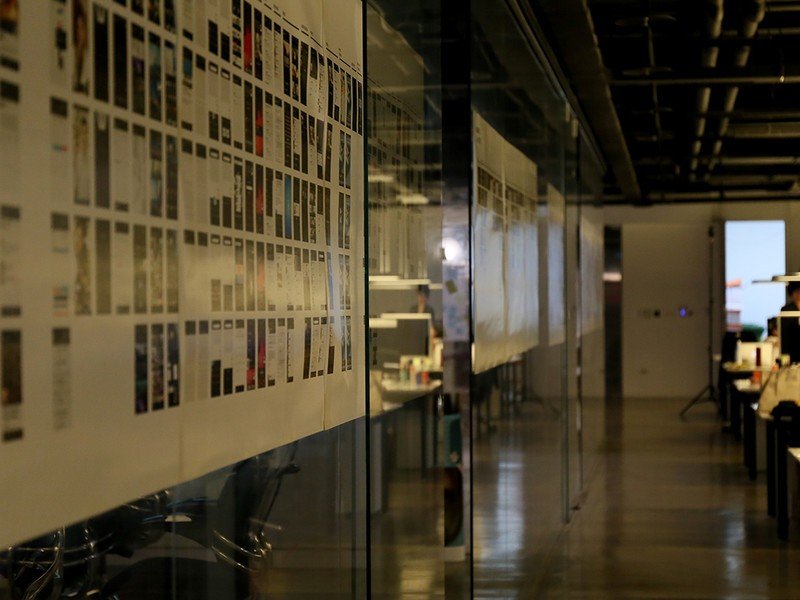
Peering inside the design headquarters
HTC's Taipei headquarters serve as the principle area for research and design, and is responsible for so much of the iconic HTC hardware over the past decade. It is here where I was able to get a glimpse at the design labs that took the U11 from drawing to prototype and finally into production. The massive building is filled with sharp right angles, copious amounts of smooth white walls, and glass that lets the light flow in from the open atrium that runs the entire height of the building.
More: Read our HTC U11 preview
For all of its excellent design nuances, the U11 still feels connected to the HTC phones of old.
The design team works away in an open office environment, in which I had the opportunity to be enamored with tables full of exploded component views of the new U11 and unreleased HTC design prototypes. (A fun one, in particular, was a prototype from ~2009 with a slide-out game pad that looked similar to an HTC Legend.) All three phones in the U series have a distinct glass back that is a culmination of years of working with glass in this building — and that work shows with the entirely unique colors and feeling of depth you don't find in any other glass phone.
HTC is understandably proud of its hardware design (its design awards are prominently on display), which helps you understand a bit why it hasn't taken more wild risks in recent years. The HTC U11, for all of its excellent design nuances, still feels very connected to the HTC phones of the last five years. Even if you feel HTC's look as gotten stale, you can appreciate that continuity.
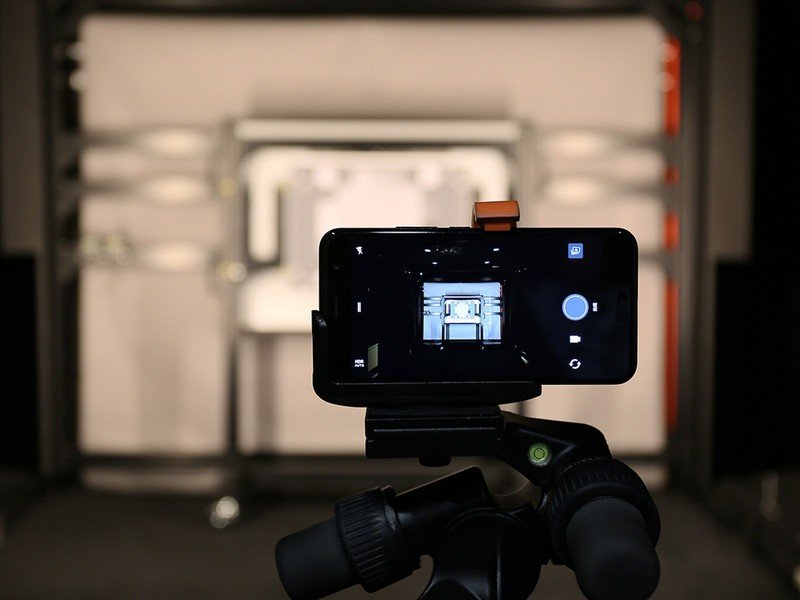
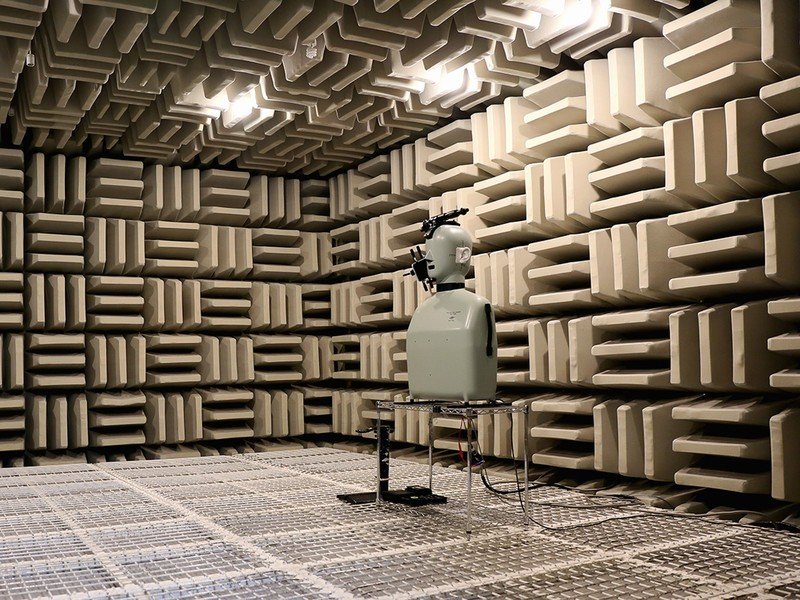
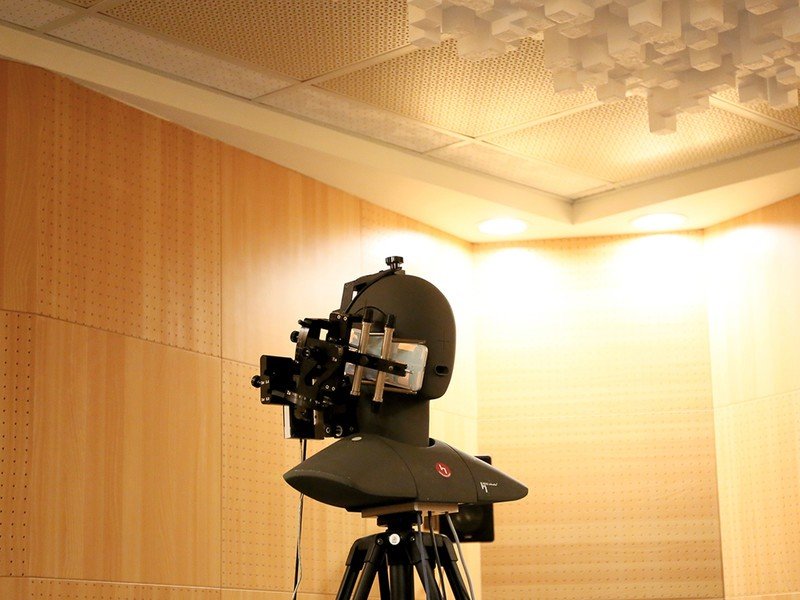
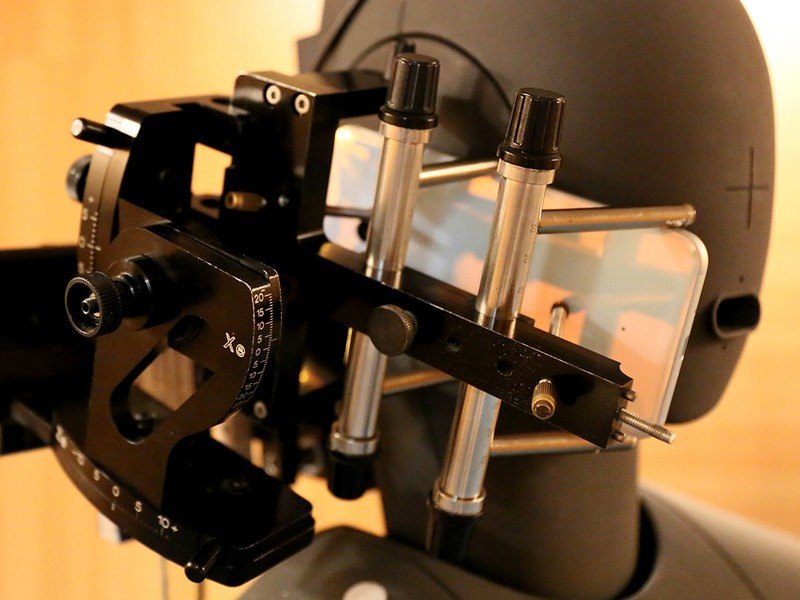
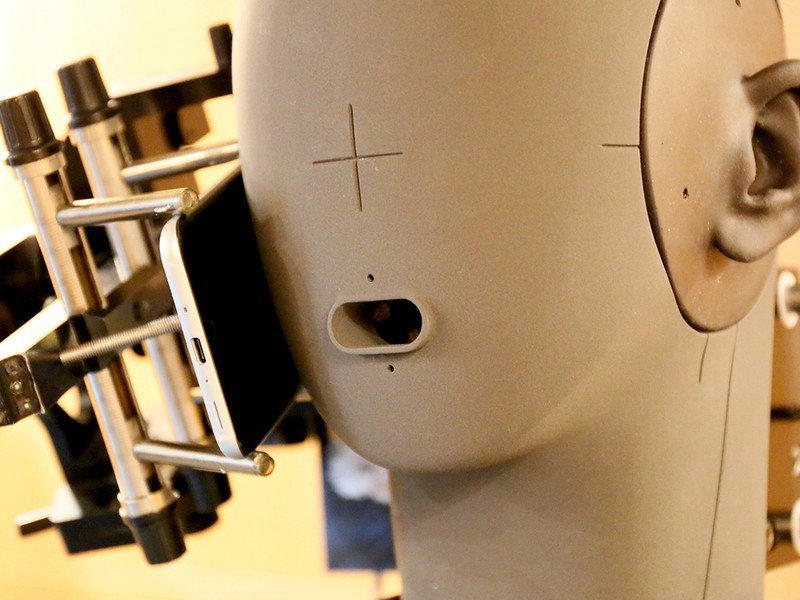
The testing that goes into individual components
Down the street from the headquarters, HTC has another building dedicated to finely tuning some of the individual components of the phones such as the speakers and cameras. Full departments for testing and developing audio equipment are here, including massive specialty anechoic chambers. The work here ranges from development of individual speaker hardware to tuning the experience of phone calls and headphones in a variety of simulated audio environments.
Be an expert in 5 minutes
Get the latest news from Android Central, your trusted companion in the world of Android
Testing individual components isn't glamorous, but it's immensely important.
Down the hall you'll find the camera lab, which beyond feeling extremely odd thanks to its black floor, black walls and blackout curtains (to mitigate glare) is an extremely important area to the fine tuning of the camera processing. Purpose-built machines test how the camera firmware interprets different lighting conditions, colors and real-world scenes, giving feedback on how engineers can tweak individual parts. HTC's camera engineers say their goal is to start with the base line of making the cameras reflect the real world as accurately as possible, then make slight adjustments sot he images continue to be appealing to the human eye.
More: HTC U11 specs
Apparently the work has paid off: HTC is touting that the U11's rear camera has the best-ever mobile DxOMark Mobile score of 90, one point higher than the Google Pixel. We'll have to see how it translates into the real world.
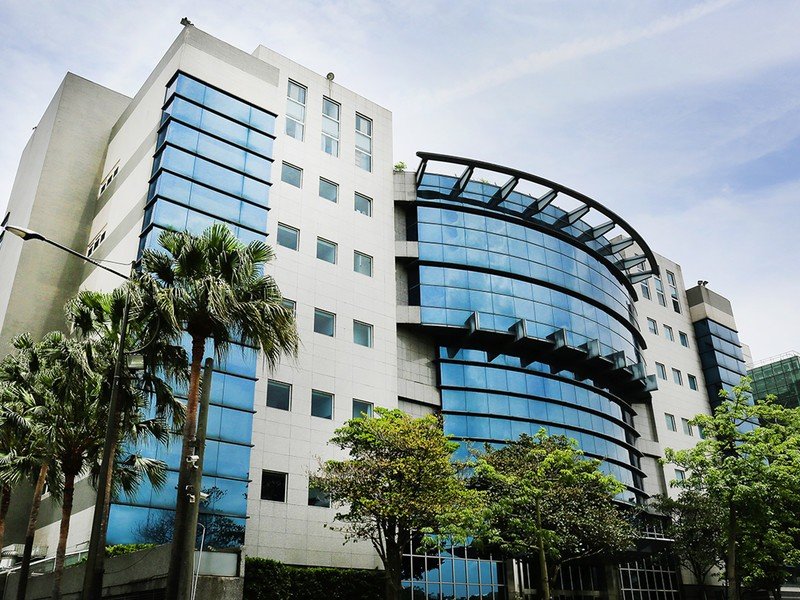
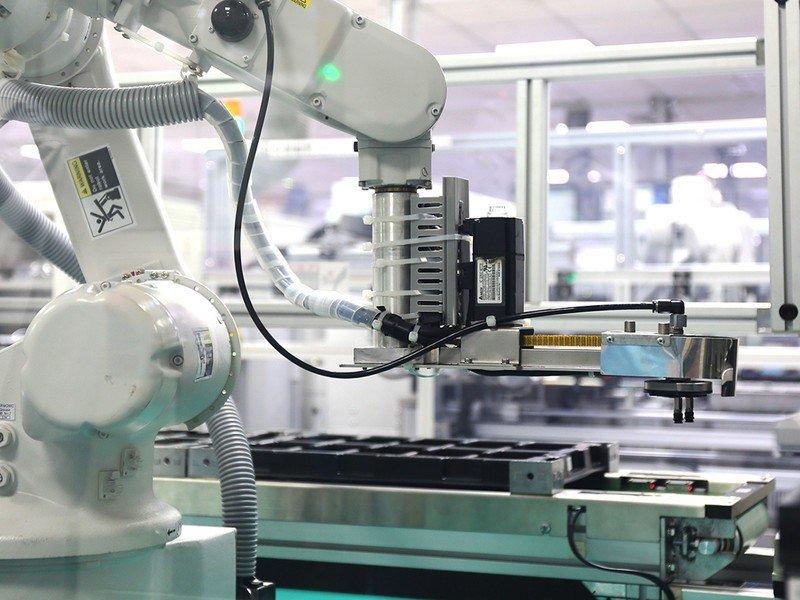
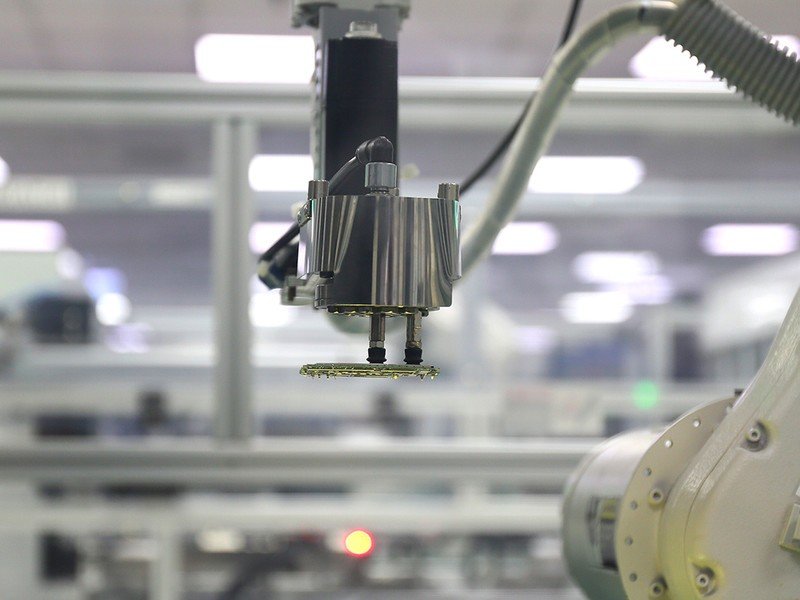
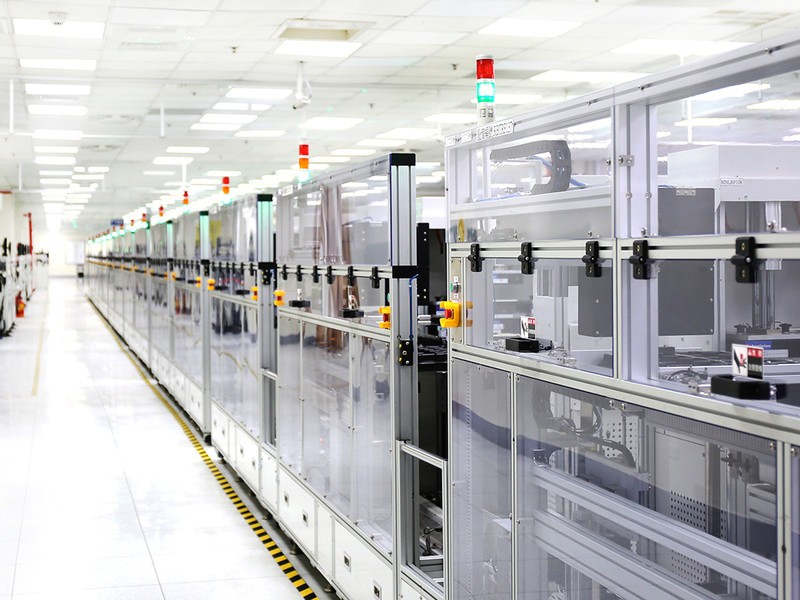
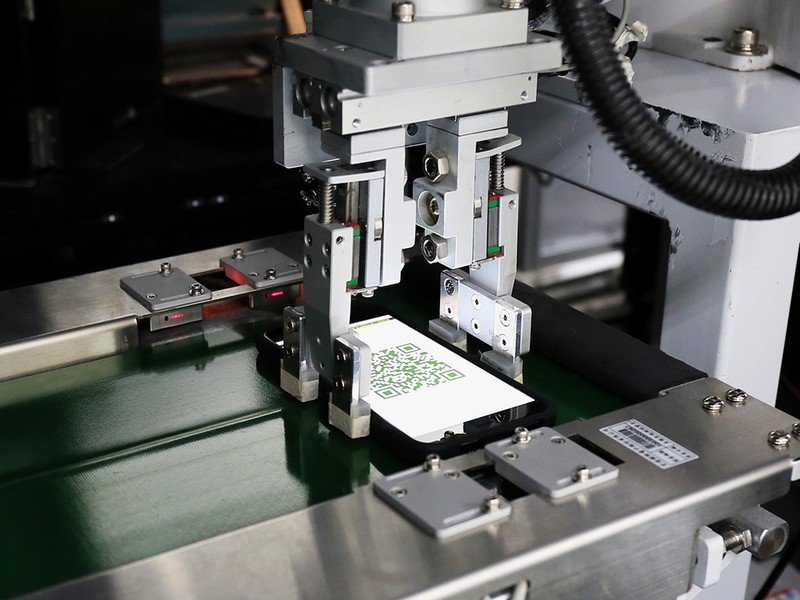
From components to completed phone in one building
About 45 minutes outside of Taipei, in Taoyuan City, HTC's manufacturing facility stands tall in dark glass and concrete surrounded by otherwise typical low-rise city buildings. Inside, I watched U11s being built — moving from sheets of individual components all the way to complete assembly and testing.
The primary components of the phones are assembled in one long line, primarily by automated machines controlled by just a handful of people. Sheets of processors, connectors, memory units and other tiny pieces are placed on main boards, which are originally attached in sets of four. After some careful placement, they're fed into a huge nitrogen reflow oven to effectively bake the components together so they're all soldered in place.
A series of custom-built robotic arms scour through the incoming flow of main boards, separating them and performing various tasks before handing the boards off to the next position. At the end of the line, taking just a handful of minutes per board, a near-complete internal assembly comes out.
Test, test and test again — the production line strives for perfection.
One floor up, the assembled internal components move to a distinctly more human-run line for final assembly. The production line is marked "OCN," coinciding with the "Ocean" codename for the U11. A couple dozen workers per line methodically piece together their selected components, while visually inspecting and scanning each one before placing it in the U11's frame. Several steps down the line, with the phones sealed, a "pre-test" section of the line tumble-tests every phone — placing the phone in a rubber protective case, it's tumbled in a machine 30 times over to test that internal components are securely attached. After completing the tumble test, their water resistance is tested with fine air jets. It is only after passing this pre-testing process that the phones go through a rigorous automated machine testing of the screen, ports, radios and cameras. The phones have the appropriate software flashed, and they're packaged.
One in 10 phones are selected for a completely new round of extra testing, in which a worker actually boots up the device, performing dozens of additional tests simulating real-world use. If a single flaw is found, the entire batch of phones surrounding it is removed from the line.
And then the HTC U11 is ready for you
A one-day tour of HTC's facilities is incredibly insightful, although it still dramatically sells short the amount of time and energy that has gone into the production of the U11. Production cycles for these phones typically last at least a year, meaning as the U11 is released to the world its successor is already under development.
But by seeing all of the individual pieces (figuratively and literally) coming together, you can appreciate the amazing amount of work that goes into making a modern smartphone that fulfills all of our needs and desires.
Ed. note: Due to tight restrictions on photography inside its production facilities, photos used in this article are all pre-approved by HTC for publication.
Our HTC U11 preview
Now that you've seen how the HTC U11 was made, you'll want to know how it all comes together. Be sure to read our full HTC U11 hands-on preview to see everything HTC's 2017 flagship has to offer.
Andrew was an Executive Editor, U.S. at Android Central between 2012 and 2020.